- Published 15 Nov 2023
- Last Modified 26 Feb 2024
- 7 min
Maintenance and Automation
There are numerous types of automation that are making maintenance more effective, from ultrasonic monitoring to robots that work alongside people. Read our guide to find out how automation technology is helping engineers predict failure before it happens, maximise machinery uptime, and reduce costs.
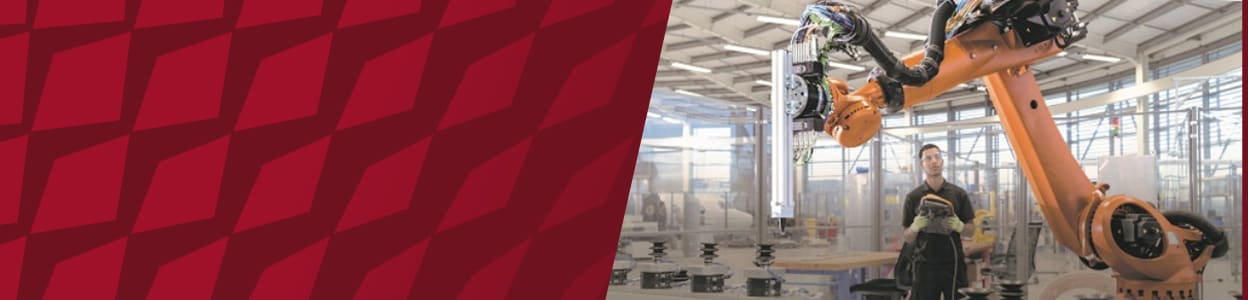
Automation technology is making a huge impact on industrial maintenance. Automation trends in maintenance include using condition monitoring sensors, vibration monitoring sensors, ultrasonic monitoring equipment and thermography equipment for predictive maintenance. Read our guide to learn how to implement condition monitoring and other forms of maintenance automation such as CMMS systems, and what the benefits of automation technology are in maintenance solutions.
Condition Monitoring
What is condition monitoring? It is the key automation trend in maintenance. It relies on networks of condition monitoring sensors such as vibration monitoring sensors, ultrasonic monitoring, or thermography equipment. These assess the condition of production machinery and detect any anomalies that could indicate a fault. By doing this, condition monitoring enables engineers to predict failure of a machine before it occurs (predictive maintenance). This automation technology helps to avoid unplanned machinery downtime, which can be very costly for manufacturers.
Types of Condition Monitoring
There are a number of different types of condition monitoring automation technology on the market that are used in different ways to enable predictive maintenance. They include vibration monitoring, ultrasonic monitoring, thermography, oil analysis, and motor circuit analysis. Let’s take a closer look at these types of condition monitoring - how they work, and what they enable engineers to do.
Vibration Monitoring
Vibration monitoring is a form of maintenance automation that analyses machinery vibration levels using networks of vibration monitoring sensors. Vibration monitoring assesses patterns in vibration signals. When abnormal vibrations occur, they may indicate that failure or malfunction of the machine is imminent. That means technicians and engineers should intervene to fix the problem before it results in failure or damage.
Typical causes of anomalies in vibration include imbalance, looseness, misalignment, and wear and tear. For example, imbalance increasing with rotational speed also increases vibration. These vibrations may reduce the life of bearings or cause other types of damage such as structural damage.
Because of this, monitoring the vibration of equipment, especially rotating equipment, is a key component of predictive maintenance, an important maintenance automation trend.
Benefits of vibration monitoring for maintenance automation include:
- Increased machinery lifespan. Engineers can increase returns on investment in capital equipment by extending machinery life.
- Improved reliability. Networks of vibration monitoring sensors relay information that allows technicians to fix problems before they become serious.
- Maximised productivity. Because machinery is more reliable, it operates for longer, and produces more than it would otherwise.
- Minimised downtime. Unplanned and reactive maintenance is reduced for the manufacturer.
Ultrasonic Monitoring
Ultrasonic monitoring uses equipment to detect mechanical and electrical faults. It works by detecting subtle changes in sound that are inaudible to the human ear but may indicate a problem with a piece of equipment. Ultrasonic monitoring equipment is often used for compressed air leak detection or to detect problems with bearings. It takes variations in sound and converts them into audible signals a technician can hear and view on a display.
Ultrasonic monitoring equipment may be used for:
- Detecting cavitation in pumps.
- Assessing compressor valve leakage.
- Steam trap maintenance.
- Detecting faulty gears.
- Other gas or fluid leaks.
- Mechanical and electrical inspection.
- Arc flash detection.
Thermography
Thermography equipment for maintenance detects faults in mechanical or electrical equipment by monitoring changes in temperature. An increase in heat is sometimes an indication that equipment is failing. Machinery can be inspected with a thermal imaging camera to spot abnormalities.
Infrared thermography equipment is often used to monitor heat coming from pipes, motors, bearings, heat exchangers, and fans. The detection of hot spots in cables, wires, control panels, and terminals may reveal problems like overloads of current or corroded terminals.
Like vibration monitoring, thermography enables predictive maintenance by using information about temperature fluctuation to detect issues that could lead to machinery downtime, allowing engineers to intervene.
Oil Analysis
The condition of a lubricant sometimes indicates a problem that may lead to machinery failing. Oil analysis assesses an oil’s composition and any contaminants, such as tiny pieces of metal, to assess the health of the lubricant and the machinery it is used in. Oil analysis reduces risk and reactive maintenance. It prevents damage to machinery, improves reliability, and reduces costs as part of a predictive maintenance regime.
Oil analysis can help determine the remaining life of the oil and whether the correct oil is being used for the piece of machinery. It can identify whether viscosity is different from what it should be. Oil analysis will also determine whether the oil is clean. Debris in the oil may indicate the severity of wear and tear to machinery and which components are degrading.
Motor Circuit Analysis
Motor circuit analysis helps technicians understand the health of motors by analysing electrical imbalances and degradation of insulation. During the motor’s lifetime, trends in motor current or voltage enable the engineer to detect damage, overheating, or excessive vibration.
Motor circuit analysis monitors current and frequency response, insulation resistance, circuit resistance, impedance, inductance and phase angle to determine motor health. Issues that may be revealed include defects in motor winding and cable and rotor defects. As with other condition monitoring automation technology, motor circuit analysis can help to predict failure before it takes place.
CMMS
The computerised maintenance management system (CMMS) is one of a number of digital maintenance automation technologies that help engineers carry out both planned (preventative) and predictive maintenance.
A CMMS is software that gathers maintenance information in a central database. Computerised maintenance management systems help optimise maintenance schedules and availability of machinery. A CMMS contains an asset registry that stores information about critical production equipment including manufacturer, model, serial number, warranty information, documentation and manuals, location, and performance statistics.
One of the principal jobs of the CMMS is to schedule maintenance correctly. The system also allocates resources such as technicians to specific tasks, records downtime and associated costs, and automates the generation of maintenance tasks, making the CMMS an important tool for preventative maintenance.
Engineers should consider a number of factors before implementing a CMMS. This includes which machinery needs to be included on the asset register, the budget available for the software, and how the maintenance team will migrate to using the system. They should look at which features are necessary to include to enable the plant to run as efficiently and effectively as possible.
AI and Machine Learning
AI and maintenance are complementary because artificial intelligence can help to analyse all the condition monitoring data collected by the engineer. This includes historical data and data that’s generated in real time. AI helps technicians understand anomalies and what maintenance is required for different pieces of equipment.
Machine learning is used to recognise and predict potential equipment failure. That enables the engineer to intervene before catastrophic failure takes place. Doing so reduces machinery downtime and maximises productivity.
Digital Twins
It’s now possible to simulate maintenance activities in a digital twin. What is a digital twin? It’s nothing less than a complete digital model of a manufacturing facility or a system. In manufacturing, digital twins help optimise the entire manufacturing lifecycle, including design, production, and maintenance. The digital twin can be used to optimise machinery without having to make actual changes at the plant and to predict faults in a simulated setting. What engineers have learned from the twin can then be applied in a physical environment to improve processes.
Co-bots
Workplace automation, co-bots and maintenance go hand-in-hand. Collaborative robots are robots that work with people to do things that are difficult and dangerous, or tasks that are physically stressful or fatiguing. These robots can also work in hazardous environments without endangering personnel. So, co-bots are likely to become more and more prevalent in maintenance to reach the parts that are difficult or arduous for humans to reach.
All of these types of automation technology are part of the development of the fourth industrial revolution that is taking place in manufacturing. You can learn more about the Industrial Internet of Things with our IIoT guide.
You can also contact RS to find out more about condition monitoring. Our experts are on hand to help.
Learn more about the many types of maintenance solutions RS offers here.
Related Articles
Related links
- Maintenance Using Vibration Analysis and Condition Monitoring
- Condition Monitoring and Predictive Maintenance
- Condition Monitoring: What Happens & When
- From condition monitoring to condition based maintenance
- Condition Monitoring
- RS Condition Monitoring Solutions
- Condition Monitoring Grinds Real Results For Coffee Manufacturer
- Seeed Studio Grove - Electricity Sensor Sensor Board Alternating...