- Published 9 Aug 2023
- Last Modified 9 Aug 2023
- 6 min
How to Use Thread-Forming Taps
When you need thread-cutting tools to connect bolts and screws to your equipment, RS carries threading taps of all standard thread types and sizes for a range of materials and thicknesses.

Want to know your spiral point tap from your taper? Thread taps are incredibly useful tools for making fixing points for bolts and can be found across all levels of industry. If you need a custom thread or bolt size after stripping the thread on an existing bolt hole, a thread tap is what you’ll need.
What is a Thread Tap Used for?
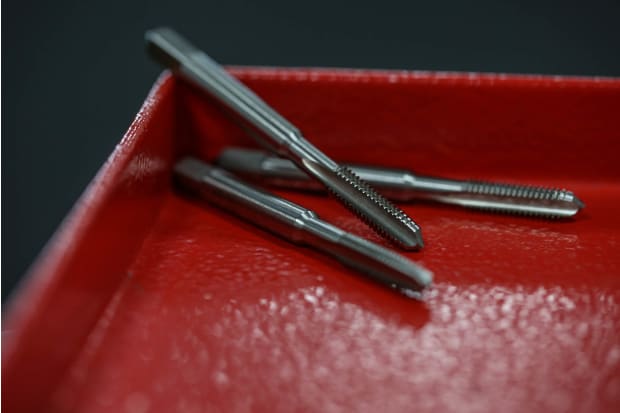
Thread taps produce holes for threaded fasteners such as bolts and screws. Just as spinning drill bits cut holes into the material, turning thread taps creates threads in pre-drilled holes. Tapping threads can be done by hand, unlike most drilling.
To use thread taps, affix them to either tap wrenches or to power tools such as drill presses or hand drills. Then, turn them into a drilled hole at the appropriate feed rate for your application.
While thread taps create the threads for the female portion of the threaded connection, such as on a nut or a hole in a workpiece, thread dies create the threads for the male portion, as with bolts or screws.
Types of Thread Taps
Along with the diameter and thread type (BSP, UNC, metric, etc.) of the holes you need to produce, you must also determine the best end point, taper, and flutings for your thread taps based on your application.
The tap’s end point can be formed with a short twist in the threads, as seen on high-performing spiral point taps. The thread tap’s taper is the slope at its cutting end. Taps with the longest tapers are taper taps. Plug taps have shorter tapers and bottoming taps have none. A given tapped hole will often require using more than 1 of these to fully complete its threads.
Flutings are the void sections cut out of tap threads. Choose a fluting style based on the types of chips your workpiece’s material will form as it’s cut. Straight flute taps are meant for more brittle material, which forms fine chips, while spiral flute taps can handle the stringy chips that softer material forms.
Taps can also create threads by cutting material away or compressing and deforming material without cutting chips. This latter process involves forming taps.
Whatever your application is in these categories, RS offers a thread-tapping tool to achieve it.
Spiral Point Tap
Choose spiral point taps for through holes since chips will travel with the tap and out of the hole.
These taps are also generally stronger and can be run at higher speeds with superior performance.
Taper Taps
Taper taps have a long slope at their cutting tip. This usually covers the first 7 to 10 threads.
These are typically used to start threads off, but not finish them. The long taper will leave the bottom portion of a hole unthreaded, requiring other taps, like plug taps, to complete the threads.
Taper taps can be used for through-holes, though, since you can push the tap all the way through and apply threads throughout (provided the tap is longer than the material’s thickness). Blind holes, however, will need to be finished with plug taps or bottoming taps after the taper tap cuts the thread’s first pass.
However, if there is enough material thickness for a non-threaded hole portion below blind threads, a taper tap alone can suffice if that non-threaded zone is longer than the tap’s sloped section.
Plug Taps
Plug tap slopes are shorter - just the first 3 to 5 threads. These let you finish blind holes’ threads started with taper taps. Use plug taps for tap repair or re-cutting threads since they don’t have to cut fresh threads, as with taper taps.
Bottoming taps have no sloped end at all. This allows cutting fully threaded blind holes.
Since completing threaded holes often requires multiple taper styles, investing in a threading tap set will keep these options close at hand.
Spiral Flute Taps
Spiral flute taps have helical flutings, like standard drill bits. As with drill bits, these flutings allow chips to travel up and out of the hole. Chips can only travel upwards in blind holes, making spiral flute taps ideal for tapping their threads.
Given this, spiral flute taps are suitable for softer materials, like ductile steel, that form ‘strings’ of material as they’re cut. The taps themselves can be less durable, though, due to the significant material removed to create the flutings.
Straight flute taps, however, have straight flutings along the full working length of the tap, giving the tap a more even cross-section and a sturdier structure. These taps are commonly designed for materials that are cut into tiny chips, like cast iron.
Forming Taps
The cutting taps discussed so far cut material away. Forming taps deform threads into material. This is best suited to soft materials like aluminium or soft steel. Since there are no chips to remove, there are no flutings.
Forming threads requires more energy than cutting threads, and this means higher costs, but the threads produced are generally stronger than cut threads. This is because the forming process compresses the material into the base of each thread, making those thin spots denser and stronger.
Cutting taps, on the other hand, weaken the material grains to an extent, leaving the threads at more risk of failure - thread stripping. That is something dreaded and avoided by anyone who’s worked with threaded fasteners.
How to Use Tap and Die Set
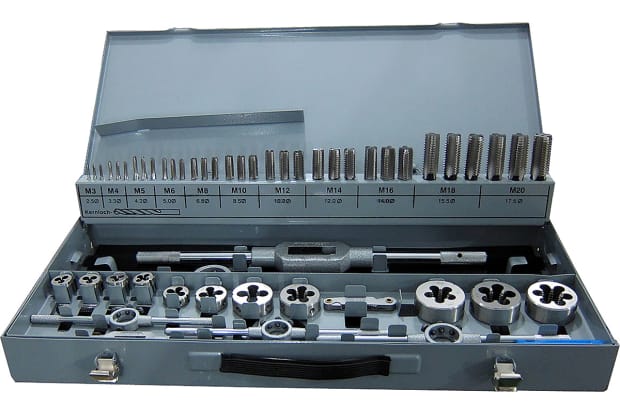
Threading tap sets are kits of all the thread-cutting tools you need for tapping holes, as well as making threads for bolts and screws.
Each kit provides thread taps for a range of hole sizes. This can include taper, plug, and bottoming taps to allow you to produce complete, useable threaded holes and to perform whatever tap repair a threaded hole may need.
Tap and die sets also come with the necessary tap and die wrenches for gripping and turning the taps and dies. To use a threading tap, affix it to one of these tap wrenches or to a power tool such as a drill press. Using cutting oil with a thread tap is a best practice to keep the materials cool and allow the tap to cut threads cleanly.
One of the most useful tools and a lifesaver if you’ve overtightened a bolt, take a look at our full thread tap range and find the right tool for you.