- Published 27 Nov 2023
- Last Modified 27 Nov 2023
- 6 min
How to Maintain Industrial Cooling Systems
Today’s industrial cooling systems are as advanced and varied as the industries that rely on them, though they do need careful maintenance to function properly.
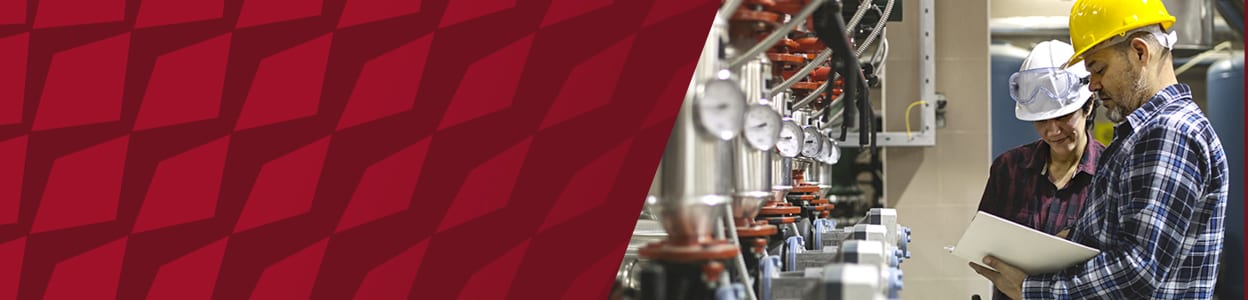
All industrial processes have ideal operating temperatures, and doing work produces heat due to unavoidable inefficiencies. There are many types of industrial cooling systems to combat this. Learn which are best for your business and how to maximise the return on investment through industrial cooling systems maintenance.
Why is Effective Industrial Cooling Important?
In industry, heat often represents energy that was consumed and paid for but did not produce useful work. Machines that run too hot are less efficient and break down more quickly due to increased stress. Overheated equipment is also unsafe to be around, can give off noxious fumes from material wear, or may even catch fire. With the right well-maintained industrial cooling systems, you can purge heat that builds – and keep things cooler to begin with.
Production of goods with tight temperature constraints, like foods and industrial chemicals, needs precise, controllable cooling. Food, beverages, and many vital medicines also need careful temperature control maintained through every stage of transportation. All this is made possible through industrial cooling equipment.
Cloud computer servers and data centres also require constant cooling. Electronics heating & cooling components accomplish this with the same heat exchanging principles seen in standard air conditioners and industrial chillers.
Types of Industrial Cooling Systems
Process Cooling Systems: This is the cooling of industrial processes that require precise temperatures achieved on-demand. For example, rapid cooling is essential in brewing beer in order to prevent off-flavours and microbes from forming. Process cooling systems have high configurability for setting the temperatures and flow rates you need. They contrast with ‘comfort cooling’ of living spaces, which is important, but has looser temperature targets that take longer to reach.
Passive Cooling Systems: Long before refrigeration, humans learned to use natural heat sinks in building design. Passive cooling systems lower indoor temperatures without expending much energy. This involves using the right materials and thicknesses for walls, strategic shade, and bending natural airflow to your will. Consider your location, environment, and overnight temperatures. Cycling in cooler air after-hours can significantly reduce your building’s thermal mass.
Portable Cooling Systems: RS carries air conditioners, air coolers, and fans that can be placed to your liking in office and industrial areas. All portable cooling systems need a plan for directing the removed heat. Be it through a window duct or hot air directed to a different room, cooling can only happen appreciably when heat is truly removed rather than just swirled around.
Evaporative Cooling Systems: Air coolers, or ‘swamp coolers,’ cool rooms by continuously drawing in fresh air and passing it over moist cooling pads. This produces a cooling effect from the added water vapour in the environment. Evaporative cooling systems use less energy than refrigeration (air conditioners), but they need frequent maintenance, chiefly in changing their pads and purging their water systems to prevent odours and bacterial growth.
Misting Cooling Systems: Commonly used in restaurant patios and outdoor festivals, misting cooling systems are a pleasant, unobtrusive form of cooling. Pumping water droplets out of high-pressure nozzles can cool environments without humidity increasing uncomfortably. They can play a part in industrial cooling by lowering temperatures of warehouses and storage facilities and even cooling transformers for electrical transmission.
Industrial Cooling Water Systems: Water is a more efficient medium than air for picking up and dispersing waste heat, and many industrial facilities are placed near water bodies to take advantage of this. Cooling towers continuously pump enormous quantities of water to remove heat from industrial processes. Oil refineries, chemical plants, and power stations (especially nuclear ones) all rely on these industrial cooling water systems.
Potential Problems with Industrial Cooling Systems
Leakage: Most industrial cooling systems pump liquids to transfer heat, but this means there are many potential leak points. Be aware of where they are, how to check and access them, and how to mitigate leak risks by using drainage traps and minimising leak points above walking zones.
Leaks that aren’t addressed can cause serious damage to your building over time, so ensure your facilities maintenance involves thoroughly inspecting common leakage areas:
- Poor insulation in ducts can mean puddles form inside due to condensation.
- Plugged condensate drainage lines could mean backed-up water finds other ways out.
- Ice build-up on evaporator coils melts when the system is offline. Ice buildup can come from clogged air filters preventing vapour from escaping or refrigerant leakage lowering performance.
Leaking refrigerant should be prevented. Though a system’s refrigerant ‘charge’ can last a few years without needing refilling, leaks do occur. Vibrating equipment and long-term equipment corrosion can cause refrigerant to seep into your business’s airflow as a gas you can scarcely detect—other than by the dizziness, headaches, and other more serious health problems breathing it in can cause. A system low on refrigerant will also struggle to cool efficiently or at all. Monitor this with instruments and regular inspection.
Frosting: Frost buildup on evaporator coils prevents heat transfer and blocks airflow, both of which kill the cooling capacity, and produce leaks—a nuisance and a danger. Regular defrosting is thus a necessary part of industrial cooling systems maintenance.
Industrial cooling equipment such as chillers often have defrosting capabilities, either automatic or manual. Understand how your units’ defrost cycles work and plan how often to run them. Defrosting often consumes energy, such as by running electric heaters, and makes cooling temporarily unavailable.
Buildup: Water carries minerals just as well as it carries heat. It’s also a building block of life. Components it flows through (as a liquid or vapour) are thus at risk of building up corrosion, scale, or bacteria and mould, so be sure to inspect and clean out these deposits regularly. They prevent heat transfer and are a health risk.
Faulty Instruments: Industrial cooling systems typically use instrumentation so you know when they’ve cooled to their target temperatures. You’ll also rely on instruments for monitoring your systems as you develop more detailed and predictive maintenance. Regular calibration is thus essential for cooling systems maintenance.
Tips for Maintaining Industrial Cooling Systems
Here are some general steps to include in a healthy cooling systems maintenance regimen, though you should always tailor your maintenance plan to your equipment’s needs.
Inspect
- Visually inspect all equipment.
- Check fan belt tension.
- Check for fluid leaks, especially in refrigerant lines.
- Listen for unusual noises and vibrations.
- Sniff for unpleasant odours.
- Verify vents open and close when required.
- Verify enclosures are secure (from rodents, etc.).
Replace
- Replace all filters.
- Replace leaking or damaged seals and gaskets.
- Replace cooling pads.
- Replace or refill air conditioner refrigerant. (‘Recharge’ the system.)
Lubricate
- Lubricate any moving parts that require it, such as fan drive mechanisms.
- Refill or replace compressor oil.
Clean
- Clean ducts.
- Clean air entry and exit points.
- Clean coils on evaporators and condensers.
- Clean drainage lines, strainers, and traps.
- Clean fan blades.
Test
- Test airflow rates.
- Test thermostat responsiveness.
- Calibrate instruments that require it.
Browse our maintenance solutions to develop the right industrial cooling systems maintenance for your business.