- Published 19 Oct 2023
- Last Modified 29 Jan 2024
- 8 min
Industry 4.0 and the Future of Maintenance
The fourth industrial revolution, which sees the convergence of digital technology with manufacturing, is transforming the way companies manufacture goods – and carry out maintenance, too. Read our guide to discover how Industry 4.0 is changing machinery repair and learn how to adopt a predictive approach to maintenance using networks of sensors and Big Data.
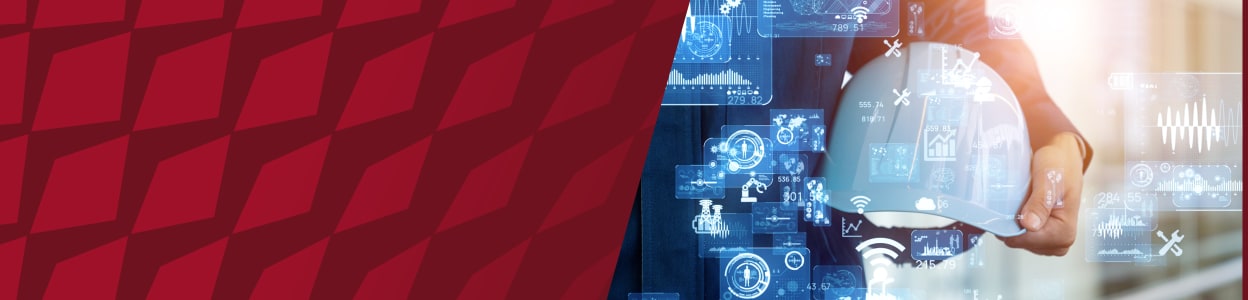
Reviewed by David Carmichael, Solution Engineer (October 2023)
Industry 4.0 encompasses a range of technologies that have implications for maintenance, from AI and machine learning to the Industrial Internet of Things, robotics, cloud computing, augmented and virtual reality. Industry 4.0 maintenance is already making use of these innovations. For example, networks of sensors and the Big Data generated by them are already being used in condition-monitoring applications across sectors, and machine learning is helping predict the need for maintenance long before machinery breaks down.
Read on to find out more about the changing landscape for maintenance technology as part of the fourth industrial revolution.
Maintenance Technology
Industry 4.0 features a number of different technologies that are changing the way in which machinery repair is carried out. Let’s look at some of these different types of tech – and how they are being used in maintenance strategies.
The Industrial Internet of Things
The Industrial Internet of Things (IIoT) is the connection of machines, products, and components to the internet in a production environment. Sensors and RFID tags on equipment and devices provide huge volumes of real-time data about condition or location, helping manufacturers manage spare parts inventory and reduce machine downtime.
Examples of the IIoT in action are condition monitoring and predictive maintenance, which are facilitated by networks of sensors on machinery that monitor performance, and collect and analyse data for engineers to make maintenance decisions. This data enables technicians to predict when machinery will fail and intervene early, an approach that differs from preventative maintenance. Preventative maintenance examples include maintaining equipment according to a regular schedule determined by the equipment manufacturer – routine maintenance – or according to its level of usage.
The IIoT is also having a massive impact on wider asset management. For example, infrastructure operators such as electricity and water networks now have the ability to connect devices all over their network using sensors and collect data indicating the health – or otherwise – of an asset. This, in turn, informs the equipment servicing activities of maintenance engineers out in the field.
Big Data
‘Big Data’ essentially means there is a lot more data from many different sources and data arrives rapidly. Having all that data opens up the possibility of solving business problems in different ways. The resources enabled by cloud computing – another important facet of Industry 4.0 – are needed to do this. Traditional computing resources wouldn’t be able to cope.
Predictive maintenance, which relies on collecting and analysing huge volumes of data from machinery, is an example of Big Data in action.
Automation
In terms of automation, the prime example of its use in Industry 4.0 maintenance is robotics. Maintenance robots are used to inspect machinery or facilities, clean up sites, and detect leaks.
The beneficial capabilities of using robots for maintenance include:
- Doing tasks that are dangerous for people to do without safety checks
- Working accurately and consistently for long periods
- Reaching areas that are tricky for personnel, such as wind turbine blades
- Taking over tasks that are tedious or time-consuming to do manually
Robots have been used to help manufacture goods for decades, but are now making their presence felt increasingly in Industry 4.0 maintenance.
Digital Twins
Digital twins are sophisticated simulations of a physical system. Engineers gather data about a real object or facility and feed that data into a digital model. It’s then possible to change and update the model to determine improvements to the object or system in question – it could be a car, factory, or aircraft, for example – and make changes to that physical system to improve it.
Advantages of this approach include speed, because it’s possible to simulate many iterations of a new system quickly to assist in product development and the design process. When it comes to Industry 4.0 maintenance, digital twins provide insights into a system’s functionality. They also enable engineers to simulate changes and see the outcome for maintenance without going to the time and expense of changing anything in a physical environment.
Predictive Maintenance
Predictive maintenance makes use of the power of the IIoT to see failure before it happens. This maintenance system has swelled in popularity in recent years, spurred on by advances in sensor technology and computing power.
Unlike routine maintenance, predictive maintenance systems identify anomalies in machinery performance to allow engineers to make repairs before damaging failures occur. This helps minimise frequency of maintenance, avoid unplanned downtime, and cut costs.
Typically, predictive maintenance will see a set of sensors installed on a machine. These sensors may detect vibration, thermal or ultrasonic information that reveals anomalies in the performance of a machine. These anomalies indicate to the engineer that a fault is developing, allowing them to intervene before it gets worse.
Predictive maintenance relies on collecting very large amounts of data (Big Data) and the ability to analyse it rapidly and make maintenance decisions. Typical problems revealed by vibration analysis, for example, include bearing failure or loose parts. Ultrasonic technology may reveal leaks in compressed air systems.
Other types of predictive maintenance technology include infrared thermography and motor circuit analysis. Infrared thermography employs cameras to measure the invisible infrared radiation emitted by a machine or component. The greater the radiation, the higher the temperature. Infrared thermography demonstrates when an asset is becoming overheated and can be used for checking electrical and mechanical faults on motors.
Motor circuit analysis, meanwhile, assesses the health of motors by revealing electrical imbalances and degradation of insulation.
These approaches are the opposite of reactive maintenance, which relies on fixing machinery when it breaks down, and differ from preventative maintenance examples because they are continuous activities rather than scheduled ones.
Benefits of Industry 4.0 for Maintenance
There are major benefits for maintenance engineers thanks to Industry 4.0 technology. They include:
Greater Efficiency
Targeted maintenance should optimise maintenance activities and reduce the need for unnecessary procedures. That makes it more efficient than traditional routine maintenance, and far more efficient than waiting for machinery to fail.
Cost Savings
Cutting machine downtime using a predictive maintenance approach saves money because a plant is more productive. Costs are also cut by making best use of the time of technicians. Finally, assets may last longer, which increases the return on investment in machinery.
Improved Reliability
Predictive maintenance identifies issues before they become problems, reducing the risk of equipment failure. This means that it makes machinery more reliable than it would otherwise be.
How Industry 4.0 Technologies can be Integrated into Maintenance Strategies
Predictive maintenance is likely to be the key area for manufacturers first starting to use Industry 4.0 technologies for maintaining equipment. A maintenance strategy should start with considering how to collect data.
Manufacturers should consider how to improve maintenance productivity and efficiency using the IIoT. The first step is to collect data from machinery. If your plan is to implement predictive maintenance, it’s important to identify critical assets to collect data from – those that are essential to the business and cause the most problems when they fail. For each machine, consider what the objective is in terms of reducing unplanned downtime and the potential return on the investment.
You also need to consider the parameters that define whether you intervene to perform maintenance. If machinery crosses an established threshold, that indicates maintenance should be carried out. For example, you might use ultrasonic sensors and determine that if a machine reaches a certain decibel level, maintenance is due. This is different from preventative maintenance, where routine maintenance is timetabled.
You must also choose your condition-monitoring sensors and install them. These could be vibration analysis sensors or thermal imaging cameras. Consider linking your IIoT devices to a computerised maintenance management system, which will allow you to monitor machinery in real time and collect, analyse, and store huge amounts of data, as well as automate work orders for maintenance, assign resources, and carry out other tasks.
Don’t forget that as your organisation embraces these cutting-edge new technologies, it’s vital that employees are kept engaged. A company with the latest technology will not get far if maintenance technicians and engineers have not bought into the Industry 4.0 vision.
Therefore, as well as considering which assets to target, how and where to collect data, and what the business case for predictive maintenance is, companies also need to factor employee engagement into their strategy.
Learn more about the RS range of automation and control equipment here.