- Published 24 Jan 2023
- Last Modified 13 Mar 2024
- 10 min
All About Machinery Lubricants
Food-safe and certified - how to find the right lubricant.

Published January 2022
Lubricants ensure a smooth process flow in mechanical engineering and in machines across all areas of production. Wherever machine parts move, bearings, chains and mechanical parts must run flawlessly. But not all lubricants are the same. Especially in food processing, only specially certified products are used. Find out which product is best suited for your machine in our guide.
What are Lubricants?
Lubricants lessen friction between material surfaces. A thin layer is applied to parts that are in direct contact with each other. This allows them to glide past each other unhindered, which in turn minimises heat generation and wear, meaning machines can be operated reliably, reducing downtime and maintenance costs. They also provide better power transmission, cooling, vibration damping, and they seal and protect against corrosion.
Further advantages of lubricants:
- Decreased friction in motors
- Controlled friction in drives
- Protection against oxidation
- Prevention of counter-threads seizing
- Remove dirt and other contaminants
- Reduce the impact high temperatures have on viscosity
- Noise reduction
- Machinery lasts longer
Requirements for Lubricants
Lubricants don't just have to lubricate well. They are subject to mechanical influences (e.g. pressure and shear stresses) and thermal effects. They must also withstand chemical interactions with other substances on surfaces and in the air and they should not succumb to ageing processes.
Where are Lubricants Used?
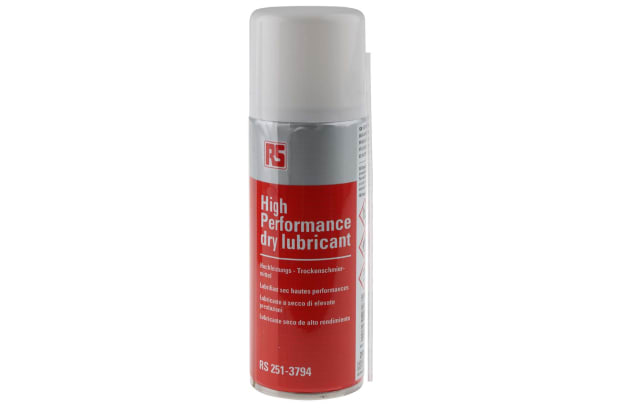
Given the different types of processes and machines, it's not surprising that lubricants come in a variety of designs. Additives often improve performance. These additives change and improve properties or even give a lubricant properties that it does not naturally have. For example, they keep hot surfaces free of deposits, diminish sludge formation from fluid impurities and protect against rust formation. They can also increase viscosity characteristics, extend flow rates at low temperatures, reduce oxidation processes, and optimise the surface tension.
In some areas of industry, they must meet special requirements to protect the consumer. If there is any chance of contact with the product in food production, or in the cosmetics, pharmaceutical, feed and tobacco industries, only certain lubricants are used. They have special properties to ensure both product safety and a smooth production process.
Types of Lubricant
Different lubricants vary in their nature:
- Solid lubricants (e.g. graphite)
- Semi-solid lubricants (greases or pastes)
- Liquid lubricants (oils and cooling lubricants)
- Gaseous lubricants (air)
In industrial environments and heavy-duty plants, mainly mineral or synthetic lubricants, greases, and synthetic oils are used.
Oil has a particularly high creeping and wetting capacity. It flows even into the smallest gaps and dissipates heat well. However, oiling limits bearing speed and reduces cooling capacity. Lubricating oils are used at high speeds and temperatures.
Grease seals against impurities such as moisture and foreign bodies and stays at the lubrication point. Industrial greases also offer better start/stop performance than machine oil. Preferred areas of implementation are roller and plain bearings, spindles, fittings, seals, guides, as well as chain drives and gears.
Pastes have a higher content of solid lubricants than greases. They are characterised by good separating, lubrication, and anti-rust qualities, even at high temperatures, under extreme pressure and in contact with aggressive media. Lubricating pastes are suitable for screw connections as well as for pressing pins, bolts, and gears.
Common Lubricant Applications
Rustproofing
Good reliability in case of material changes on the contact surfaces.
Cleaning
Remove surface impurities and oxidation of metallic contact surfaces.
Which Lubricant is Suitable for What?
In addition to multi-purpose lubricants, many types with specific properties are commercially available for a wide variety of tasks. Some examples are:
- Anti-corrosion: water-resistant and dirt-repellent with a molybdenum base
- Wire cables: dehydrating oil-based lubricant spray especially for use on wet ropes or cables
- Electronics: colourless silicone oil for lubricating, insulating, and protecting sensitive electronic components
- Chain links and chain drives: for use at high temperatures, also available for food-grade applications
- Wood: clear, PFTE based lubricant; also for cardboard, paper and textiles
- Hydraulic systems: temperature-resistant and food-safe lubricant for air compressors and hydraulic equipment
- Pneumatic tools: FPS lubricating spray for dry, non-greasy surfaces
- Hinges: there are several options for hinges, including non-toxic and biodegradable lubricants made from rapeseed oil
- Locks: grease-free, odourless, and antistatic graphite dry lubricant powder and other lubricants for locks usually come in a tube for precise administration
- Valves: metal-free and vapour-resistant high-performance lubricants with graphite/calcium fluoride formula are suitable for valves
Conditions for Lubricants in the Food Industry
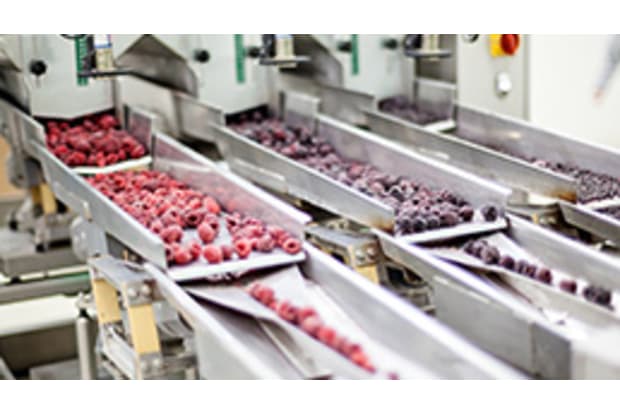
Special requirements apply to the food and beverage industry as conventional industrial lubricants will not meet strict food safety standards. They should withstand greater stress during a daily clean with water, steam and detergents, and be resistant to animal fats, blood, salts, sugar, and fruit acids. In bakery machines, the fine flour dust must not bond with the lubricant or settle in the cracks. The extreme heat used during baking and preservation or extreme cold as in the production of frozen products also pose an additional challenge.
As a result, there is a wide range of food-grade lubricants available to suit numerous uses. Finding the right one will come down to expertise and individual experience.
Approval Conditions for Lubricants in Food Processing
In cases where lubricants may have incidental food contact, food-grade grease must be used. The National Sanitation Foundation (NSF) determines which types are allowed for which purposes. The USDA also approves lubricants for the food industry. Products with an NSF-H1 certificate or USDA-H1 approval are often of the same grade. Since 2006, the ISO 21469 standard has uniformly regulated food-grade lubricants. According to the EC Directive, these regulations also apply to the production of animal feed.
Lubricants with NSF approval must be tasteless, odourless, and safe. The use of appropriate raw materials affects all components from underlying and base oils to additives and active ingredients to thickeners. They must be free of heavy metals such as zinc and barium and must not contain any organometallic EP additives (e.g. zinc or a molybdenum base). Even approved additives such as sulphur and phosphorus are often limited in their quantity.
If there is any chance of lubricants having incidental contact with food during manufacturing, only NSF-H1-certified products must be used.
Important: Even if these H1 lubricants are considered to be safe, food contamination must be ruled out at all times.
NSF Certifications for Lubricants
NSF H1: For all applications where incidental food contact is a possibility.
NSF H2: Must not come into contact with food. Suitable for all applications where there is no food contact. Free of toxic components.
NSF H3: Soluble lubricants, for example, to prevent corrosion on hooks or knives; must be wiped off before use. Must not come into contact with food.
NSF 3H: Anti-caking agents for production lines with direct or continuous contact with food. Avoid use where food packaging is made, or where food can stick to grills, baking pans or knives.
Food-Grade Base Oils
Base oils are the basis of every lubricant. The four types of food-grade oil approved for food processing are characterised by various advantages and disadvantages:
Name | Description | Advantages | Disadvantages |
---|---|---|---|
White oils and paraffin oils | Highly refined crude oil treated with bleaching oil | A particularly high degree of purity Compatible with many materials Good flow properties | Rapid ageing as there are no oxidation-inhibiting additives |
Polyalphaolefins (PAO) | Synthetic hydrocarbons with raw gasoline or propane gas base | Superior lubrication performance Resistant to oxidation and ageing Good viscosity index Low setting point Low evaporation rate | Comparatively expensive |
Ester | The chemical compound from a combination of alcohol and acid (esterification), saturated or unsaturated esters | Different forms Better natural lubricating effect than white oil Good viscosity index Saturated ester does not age | Prone to hydrolysis Not compatible with all paints and seals Relatively expensive |
Polyglycols | Polyhydric alcohols with a naphtha base | Very easily soluble in water Excellent lubricating properties High viscosity index (VI > 200) Age-resistant even at high temperatures | Not compatible with all paints and seals Not compatible with other synthetic and mineral oils |
Lubricant Standards
The standards for lubricants can be categorised as follows. Some regulate designations and others dictate minimum requirements. In addition, there is a comprehensive set of rules on the permissible test and test procedures.
Examples:
- DIN 51503 Minimum requirements for refrigeration oils
- DIN 51517 Minimum requirements for lubricating oils
- DIN 51520 Minimum requirements for cooling lubricants
- DIN 51524 Minimum requirements for hydraulic oils
Properties of Lubricants
Physical key figures describe the most important properties of lubricants and help you find the right lubricant. Which lubricant is suitable for which task depends on the material and processing steps as well as the tool surface and processing speed.
Temperature also plays an important role.
- The density of a lubricant depends on pressure and temperature. The higher the density, the greater the possible performance losses
- Viscosity: The flow properties determine the creep capacity of the lubricant. They help measure the thickness of the oil layer between two surfaces. The viscosity index describes how the viscosity changes as a function of temperature
- The aniline point indicates the lowest temperature at which the aniline and oil of the lubricant still form a mixture. Aniline serves as an additive of lubricants in the production of fuels. It is of particular importance when used in motors
- The dropping point indicates the temperature for the transition from semi-solid to a liquid state. This is important for processes with high temperature effects
- The setting point indicates the lowest temperature at which lubricant still flows. This is particularly important for cold-intensive processes
- The flash point indicates the temperature value at which a flame is immediately formed by contact with an ignition source. The focal point is slightly higher; a persistent fire can be triggered at this temperature. The temperature at which a flame is produced even without an external ignition source is called the ignition point
- The neutralising capacity indicates how much potassium hydroxide is needed to balance free acids in the oil. It is crucial for the ageing of lubricants
Good to Know!
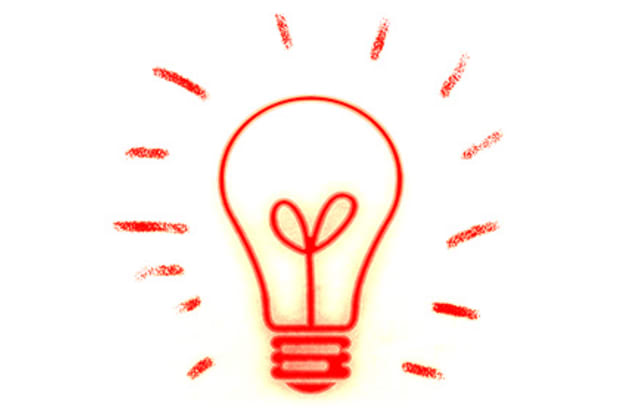
Environmentally-Friendly Lubricants
Bio-lubricates and bio-oils are environmentally friendly according to OECD 301 and are made from renewable raw materials or mineral oils free from heavy metals. The source of the base oil is vegetable or animal fats, with rapeseed oil a common component. They are used as normal lubricants in the same areas of application. In a few exceptional cases, they may be inferior to conventional mineral oils, for example where high temperatures come into play.
Popular Manufacturers & Brands
Well-known lubricant manufacturers include Ambersil, CRC, Rocol, RS PRO, SKF, and WD-40. In addition to these brands, we also stock lubricants and greases from Klüber, which are characterised by their resistance to oxidation and aggressive chemicals.
Shop Key Brands
RS PRO
With a range of different lubricant types available, our in-house brand RS PRO offers plenty of choice to meet your requirements.
CRC
No matter your required application, CRC lubricant is sure to meet your needs. Click through to shop the full range.
Ambersil
Click through to browse our full range of top-quality Ambersil lubricant products.
WD-40
Leading brand WD-40 has a wide range of lubricant products available for various tasks and applications.