- Published 29 Jan 2024
- Last Modified 29 Jan 2024
- 8 min
Maintenance Strategies in Process Manufacturing
Reduce the chaos of corrective maintenance in process manufacturing through clear maintenance strategies. Learn how total productive maintenance and reliability-centred maintenance are both versatile systems for tailoring effective service for all your equipment.
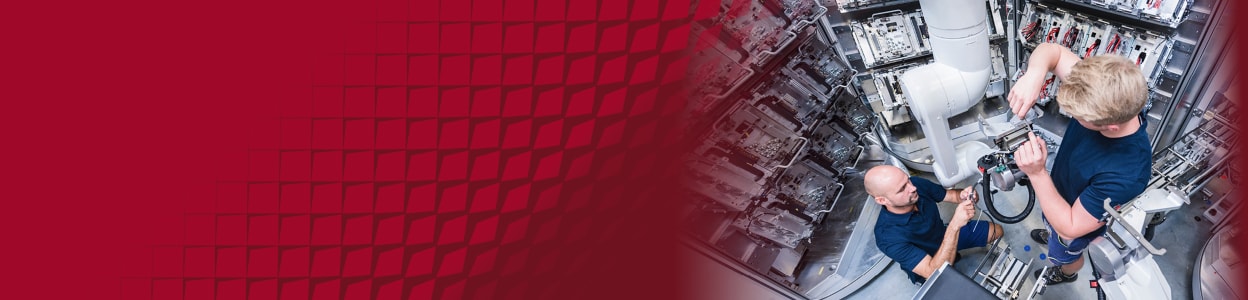
Reviewed by Karl Ralph, Technical Support Engineer (January 2024)
Maintenance in process manufacturing can be difficult to plan, given the variety of equipment in plants. Machines’ needs vary in parts cost, operating conditions, replacement frequency, and maintenance skills required. Effective maintenance strategies exist for managing all these factors, though. These include total productive maintenance, based on overall equipment effectiveness, and reliability-centred maintenance, which seeks to prevent specific modes of failure. Both have the versatility to match your facility’s complex maintenance needs.
Importance of Maintenance Planning
The importance of maintenance can’t be overstated - avoiding costs and the lost time of breakdowns, improved health and safety, and peace of mind. Thoughtful and careful planning of maintenance in turn has many benefits:
- Planning maintenance means budgeting money and personnel for equipment service intentionally rather than dealing with the costs of unanticipated replacements
- Scheduled, regular inspections uncover most problems, letting you address them before they worsen
- You’ll better understand your equipment: what it needs, what to avoid, and what it’s costing you to own and operate. Your operators will also learn to care for it better
- A clear maintenance plan produces documentation and records. You’ll have resources for investigating equipment failures - what went wrong and how to avoid it
Different Maintenance Approaches
With the variety of machinery and equipment in process manufacturing, it’s challenging to form an affordable maintenance approach for its needs. There are many types of maintenance strategies based on maintenance frequency and conditions.
Corrective maintenance waits for problems to happen and then fixes them. This is usually unacceptable in process manufacturing since it means significant downtime, costs, and the headache of diagnosing problems. However, the ‘run-to-failure’ approach of corrective maintenance can be acceptable for equipment or parts that have low replacement costs and redundancy and inventory in place.
Preventive maintenance schedules equipment for service (which means downtime) using fixed periods like dates or operating hours. This is a robust process manufacturing maintenance system that can find and address all equipment issues, but it can mean higher and more frequent ongoing maintenance costs.
Predictive maintenance has less frequent maintenance costs than preventive maintenance. Using condition based monitoring and advanced software you can ensure your assets get only the maintenance they need when they need it, reducing downtime. This system also identifies problems in their initial stages before they become more expensive to fix. Predictive maintenance does require a significant investment in instruments, software, and training, but it pays off by reducing breakdowns and their costs.
These concepts can in turn be used in broader maintenance approaches that encompass more of the company. Total productive maintenance and reliability-centred maintenance can both employ a combination of the above maintenance strategies to tailor a system to all of the company’s needs.
Total Productive Maintenance (TPM)
What is Total Productive Maintenance?
TPM empowers all parties in process manufacturing equipment to design, install, operate, and maintain them to minimise and avoid breakdowns, inefficiencies, defective output, and accidents. This broadens the commitment to effective maintenance to the whole company, not just maintenance technicians.
TPM is built around eight pillars:
- Autonomous maintenance: Empower operators to perform routine maintenance tasks on their own. Autonomous maintenance trains equipment operators to care for their machines and avoid breakdowns through daily measurements, records, lubrication, and cleaning. This also encourages operators to report issues and suggest maintenance improvements.
- Planned maintenance: Schedule maintenance for when equipment is not in use. Using predictive or preventive maintenance, monitor equipment’s performing hours and conditions to find the optimal time for a service shutdown.
- Quality maintenance: Synchronise with your quality control system by focusing on the quantity, costs, and root causes of produced defects. Adjust maintenance accordingly to improve your output.
- Focused improvement: Form small teams, drawing from different departments, to investigate recurring issues and identify small improvements to equipment operation
- Early management: Use the knowledge collected in autonomous maintenance to design and maintain new machines effectively from the start.
- Training and education: Identify the staff you’ll involve in TPM and the training they’ll need for their roles in it.
- Health, safety, environment: Strive to eliminate health and safety hazards, through both corrective and preventive actions.
- Administration: Expand TPM to non-production departments by reducing material waste and improving scheduling and procurement.
TPM is a company culture change: convincing the people involved in process manufacturing to do their part to maximise overall equipment effectiveness.
Steps of Implementing TPM
There are five steps to effectively implementing TPM:
- Select equipment: TPM doesn’t demand immediate, plant-wide adoption. Start by selecting a piece of equipment you can practically address the maintenance for and thus produce some demonstrable business benefits. This maintenance trial can be for a less crucial unit that’s easy to experiment with, a principal asset that your output relies on, or a notoriously problematic machine—you decide. Include all departments in redeveloping this asset’s maintenance
- Clean the unit up: Get the selected asset to a fully clean, functional, tuned-up starting state. Next, strive to keep it that way using the 5S system: kept organised, clean, and orderly using established, audited procedures. From there, introduce autonomous maintenance by agreeing which routine tasks operators can perform, training them as needed
- Measure current OOE: Another TPM tenet is overall equipment effectiveness (OEE). OEE considers equipment performance based on its uptime, efficiency, and quality. Record this considered unit’s instances of major shutdowns for service, minor unplanned operational pauses, and defective output - which all reduce overall equipment effectiveness. Collect at least two weeks of data, and note all reasons for unplanned stoppages, even if they’re unknown
- Address worst issues: Using small teams for focused improvement, tackle the worst stoppage from the unit’s trial. Collect and analyse evidence to determine the problem’s cause and its business effects. Discuss as a team how to prevent it and schedule a stoppage to implement this. Monitor OEE and whether this measure prevents recurrence and discuss an alternate approach if it does not. If it does work, address the second-worst problem next
- Proactively maintain: Assess the complete unit for components that can wear, fail, or form operational stress. Form maintenance strategies for all these modes of failure, such as:
- Replacement at a certain wear level, based on regular inspection
- Replacement based on predicted failure time, based on condition monitoring
- Replacement at scheduled maintenance intervals, based on operating hours
Continually assess and adjust this maintenance system through records, audits, and analysis of equipment performance.
Reliability-Centred Maintenance (RCM)
What is Reliability-Centred Maintenance?
RCM is a maintenance system structured around avoiding identified modes of failure and achieving clear performance goals. This is thus maintenance that has a clear method to measure success.
With reliability-centred maintenance, you focus on what care each of your machines needs to prevent their specific possible breakdowns. This means carefully analysing the ways each machine could fail, why and when this would happen, and how to prevent these modes of failure in a cost-effective way.
Steps of Implementing RCM
Once you’ve identified a machine’s modes of failure and their possible causes and expected frequency, develop a maintenance plan that will end up costing less than addressing those modes of failure as they happen.
- Identify candidate machines: Identify the equipment you rely on the most and assess how crucial it is for your business and what the consequences of its downtime would be. Consider factors such as:
- Cost of replacing it
- Whether it has backups on-site
- How much of a constraint it is on operations
- What it has cost you in breakdowns before: (money, lost production, stress)
- Determine modes of failure: In what ways could this machine fail to perform? This could mean:
- Not operating at all
- Operating insufficiently
- Causing a safety incident
-
Analyse reasons for failure: Think about all the possible causes for these failure modes, and how often they could happen. Each mode of failure could have more than one possible cause, such as a driveshaft’s low rpm being due to a worn belt or low grease.
-
Gauge severity: Compare each cause’s likelihood against the severity of the corresponding failure mode. Doing this with a risk priority chart with coloured zones can help visualise the significance of each of these causes.
-
Plan maintenance: Work out economic maintenance strategies for each machine to avoid each cause of its modes of failure. Consider whether you should proactively avoid these causes through predictive or preventive maintenance or if it’s truly cost-effective and safe to just run them to failure through corrective maintenance. This will ensure reliability for your assets and achieve true reliability-centred maintenance.
These maintenance strategies can greatly improve your process manufacturing. Browse RS’ maintenance solutions to learn how to maximise your overall equipment effectiveness.