- Published 30 Jan 2023
- Last Modified 22 Oct 2024
- 12 min
A Complete Guide to PAT Testing
What is PAT testing and how does it work? Learn more about PAT testers in our comprehensive guide.

Reviewed by Jay Proctor, Technical Support Team Leader (August 2021)
Ahead of any PAT testing, find out more about the PAT testing equipment you will need to use, including information on which PAT tester will be best suited to the task at hand.
What is PAT Testing?
Portable appliance testing, otherwise known as PAT testing, involves checking electrical appliances to find out whether they adhere to set safety standards.
An initial visual test is performed to inspect the condition of the equipment and cabling. Next, tests are carried out in respect of the standard of insulation, the earthing continuity, and contact with exposed metal. There are various types of PAT testing equipment, specifically designed to ascertain safety levels.
It is expected that a PAT tester will allow for the testing of earth continuity, insulation resistance, and main cord wiring. However, the majority of PAT testing appliances do not allow for mains power connectivity. Standard user-friendly PASS/FAIL testers are frequently used for professional purposes. Advanced PAT testers are recommended, however, as they offer much more data.
How Does PAT Testing Work?
The earth continuity test allows for verification of the connectivity between any exposed metal parts and the protective earth pin in the mains plug of a class 1 appliance. This involves connecting the item of electrical equipment to the PAT tester, and the test probe to exposed metal parts. A current is then transferred from the PAT tester along a mains cord to the enclosure. This current then flows back to the PAT tester via the protective earth conductor. This will result in the display of the protective earth path resistance.
Insulation testing involves connecting the tested appliance with the PAT. Typically, a test voltage of 500V DC is then applied to the mains plug terminals. This will ideally result in a high resistance reading being displayed on the PAT screen. However, insufficient insulation between the live parts and earth will result in a current flowing from the insulation to the PAT via the protective earth conductor. The low level of insulation will also be highlighted in the PAT reading.
The measurement of a predictive conductor current will require the connection of the appliance to the PAT tester. The powering of the appliance will result in a current flowing along the mains supply via live and neutral conductors. The live and neutral currents will ideally be neutral. However, the PAT may highlight an imbalance between the live and neutral currents in some instances.
What are the Different Types of PAT Testers?
PAT testing equipment has various levels of functionality. Basic PASS/FAIL kits are very easy to use and relatively inexpensive. They are the preferred choice for a range of businesses, clearly indicating whether an item of electrical equipment has passed or failed. Mains-powered testers require connection to an electrical supply. However, the self-contained battery versions are ideal for large workplaces due to their portability and ease of use. They commonly feature basic light systems that indicate whether electrical items have passed or failed the test.
Basic PAT testing equipment also allows for the establishment of:
- Earth continuity
- Insulation resistance
- Polarity
Basic PAT testers don't display the complete set of electrical test results, and neither do they allow for test configuration or data storage. However, they are often the best choice for obtaining electrical test results quickly and easily.
Advanced PAT testing kits offer the following types of functionality:
- Portable RCD lead testing
- Adjustable PASS test limits
- Substitute and mains powered leakage testing
- Fuse testing
- Lead polarity testing
Some PAT testers do display the complete set of results, while also being easily affordable. These PAT testing models are user friendly and feature basic interfaces, enabling test results to be quickly taken and recorded. Unfortunately, these PAT kits are not suitable for testing the complete range of electrical equipment. Most models also lack functionality for the configuration of test parameters.
While a 500V insulation test voltage is typical and suitable for a number of appliances, many PAT testers now include the option of a 250V insulation resistance test. This is essential for testing sensitive and surge-protected equipment, such as IT hardware.
Advanced PAT testing kits are suitable for users with a high level of technical knowledge and expertise. These advanced systems are particularly well suited to facilities management, as they allow for the recording of the location and test status of equipment and appliances. Some of these systems can also transfer the test results to computers for digital interpretation. Test records can be maintained with PAT software.
As well as individual testers, you can often buy PAT tester kits that are sourced to give you everything you need to test efficiently and safely.
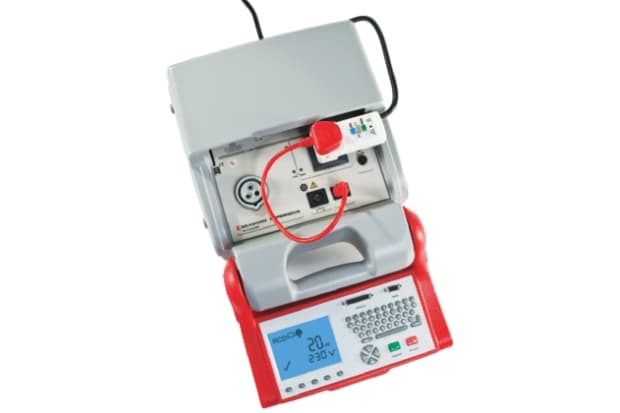
Advanced PAT Testers
These can be used with class 1, class 2 and class 3 IT equipment.
Main Benefits:
- Customisable
- Ability to test a wider range of equipment
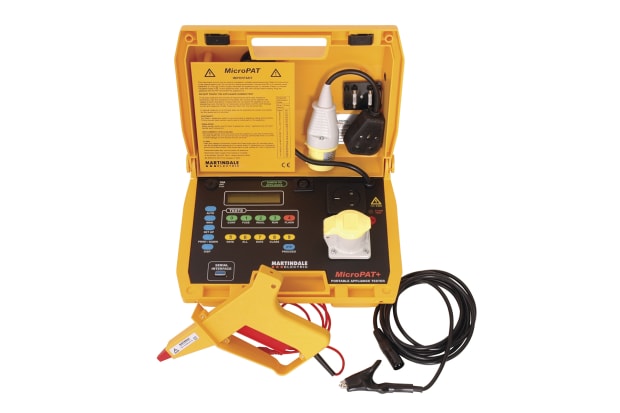
Computerised PAT Testers
These can be used with class 1 and class 2 equipment.
Main Benefits:
- Automatic and manual testing
- Flash testing capable
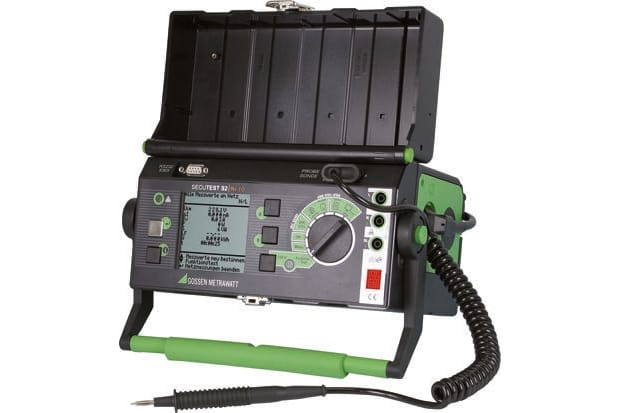
Medical Safety Testers
These are specifically for use with medical safety equipment.
Main Benefits:
- Automatic detection of protection class
- Parallel test sockets for equipment under test without mains
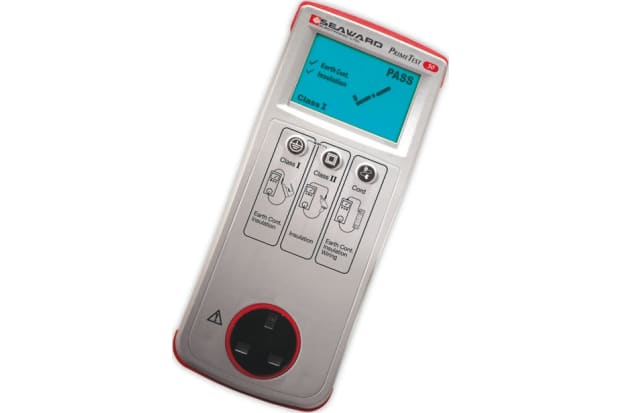
Pass/Fail PAT Testers
These can be used with class 1 and class 2 equipment.
Main Benefits:
- Automatic testing
- Simple to use
What PAT Tester Accessories Do I Need?
If you will be carrying out regular electrical testing, then investment in PAT accessories is highly recommended. Essential PAT testing accessories include:
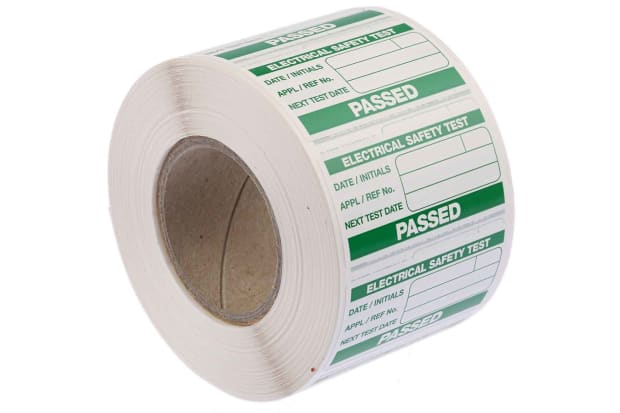
PAT Testing Labels
These labels should be attached to items that have passed the PAT test. They are made of high-quality durable materials in accordance with the regulations outlined in the IET Code of Practice.
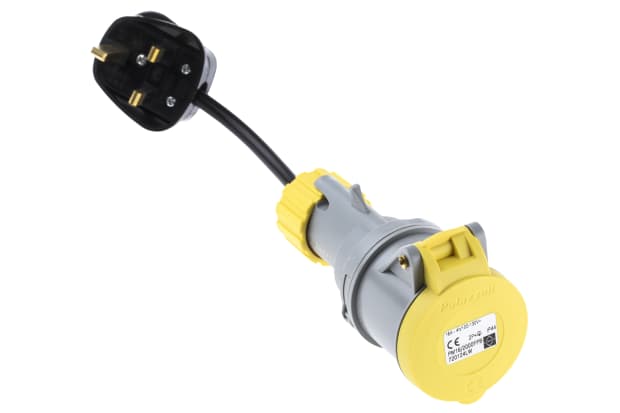
PAT Test Adapter
These adapters allow for the testing of electrical items which wouldn’t otherwise be possible. The most common variety is the IEC extension lead adapter.
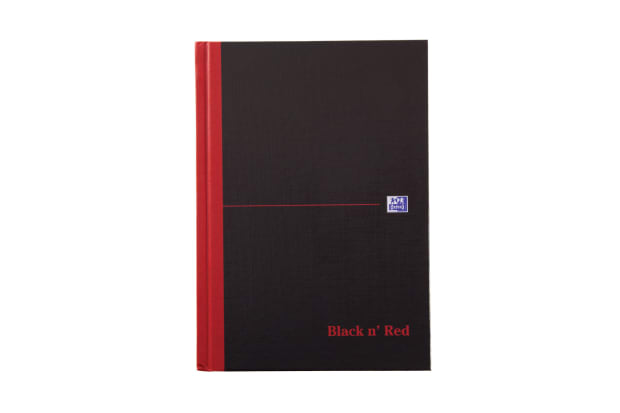
PAT Register
All your PAT testing results can be recorded in this register. It will allow you to easily compare the performance of electrical items over time.
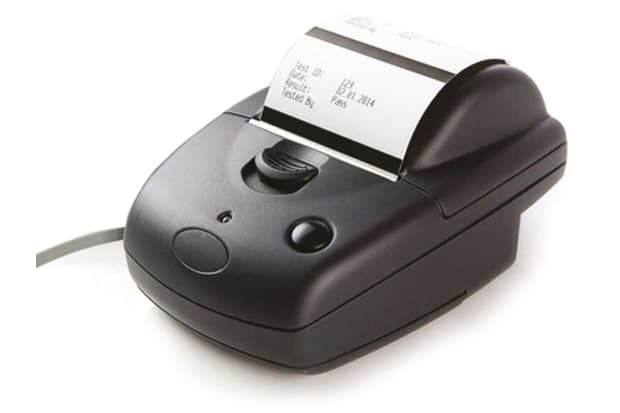
PAT Test Printer
These devices can be used to print labels featuring essential details such as the pass/fail status, barcode, test date, and the name of the individual who performed the test. Additional investment in a scanner and replacement cartridges will be necessary.
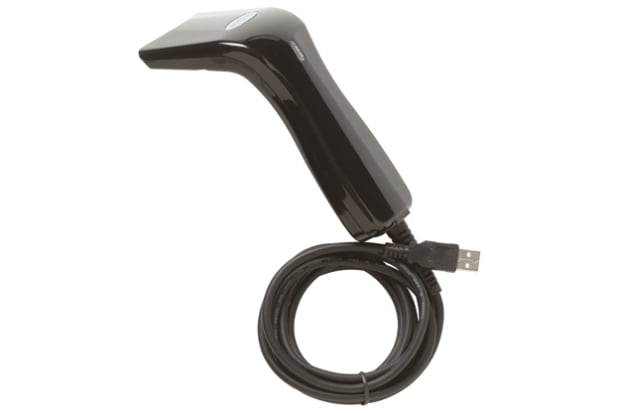
PAT Test Scanner
Barcode scanners are particularly useful when it comes to the repeat performance of PAT tests. They allow for the addition of barcodes that can feature in testing records.
What Needs to Be PAT Tested?
The electrical class and category of the item are the two main factors specific to the requirement for PAT testing. Electrical testing should be carried out in accordance with appliance classes, which are outlined in the IET code of practice. This applies to electrical equipment supplied at voltages up to and including 1000V AC or 1500V DC between conductors, or 600V AC or 900V DC between conductors and earth.
The categories of electrical equipment as defined within the IET code of practice include:
- Portable appliances or equipment
- Handheld equipment or appliances
- Movable equipment
- Stationary equipment or appliances
- Fixed equipment or appliances
- Appliances or equipment for building in
- IT equipment
- Extension leads and RCD extension leads
- Multi-way adaptors and RCD adaptors
Items such as electric drills, monitors, PCs, and kettles are all suitable for PAT testing. You should be aware that electrical appliances fall under categories I, II or III. Those in category 1 are rated as being the most dangerous, with those in category 3 being the least. The rating of the item will have a direct bearing on the need for PAT testing. You must ensure that all items in category 1 are PAT tested. Items in category 2 will only require an insulation test. However, testing won’t be necessary for items in category 3.
Examples of class 1 appliances include:
- Photocopiers
- Vending machines
- Desktop computers
- Fridges
- Microwaves
- Toasters
- Kettles
- Laptop cables
- Extension leads
Examples of class 2 appliances include:
- Hedge trimmers
- Lawnmowers
- Drills
- Food mixers
- Lamps
- Televisions
- Hairdryers
Examples of class 3 appliances include:
- Laptops
- Mobile phone chargers
- Torches
- Cameras
Popular PAT Testing Equipment Brands
PAT testing is essential to ensure that electrical items function in accordance with safety regulations. As previously mentioned, there should be some consideration of the required regularity of testing when choosing which work equipment to buy. There is a variety of recognised brands offering PAT equipment for labelling, testing, and licensing purposes.
Some popular brands include:
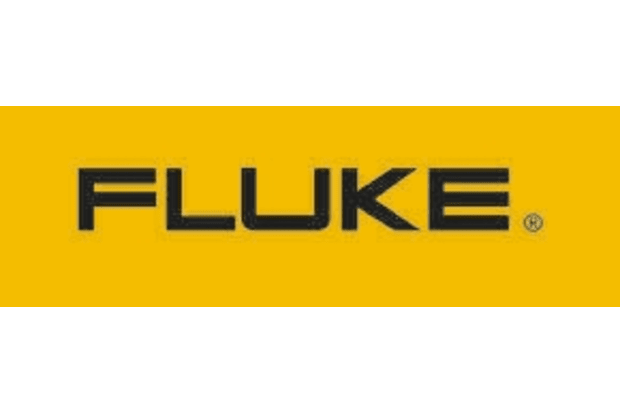
Fluke
Domestic customers and professional electricians take great confidence in the quality of testing equipment produced by Fluke. The Fluke 6500-2 and 6200-2 allow for rapid testing, with the assurance of safety.
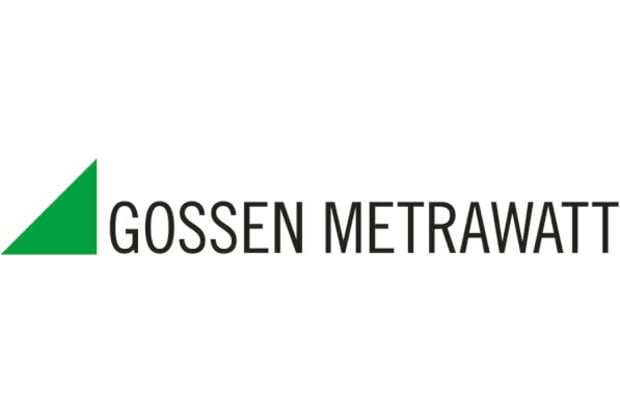
Gossen
The Gossen Metrawatt Metratester and Metrawatt Seculife are two great examples of advanced PAT testing equipment, entirely suitable for professional purposes. They allow for precise electrical testing in accordance with recognised standards such as DIN VDE 0701-0702, EN61010, and EN60950.
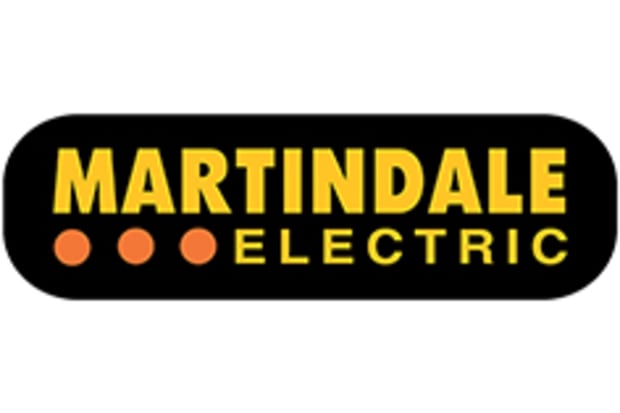
Martindale
Taking pride in the development of unique ideas and techniques, Martindale has produced a range of PAT testing equipment suitable for electricians and engineers. Whether you are interested in speed and convenience or advanced performance, Martindale has PAT testers to suit your requirements.
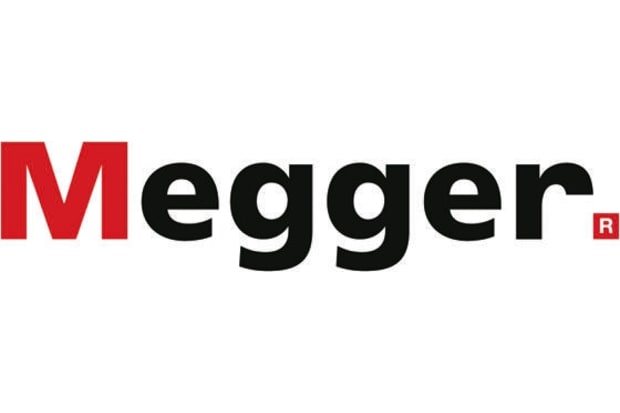
Megger
Offering a complete variety of electrical testing equipment, Megger is the preferred choice of electricians and engineers across the world. Megger testers such as the PAT120 and PAT150 have been designed for the ultimate combination of efficiency, cost reduction, and performance optimisation
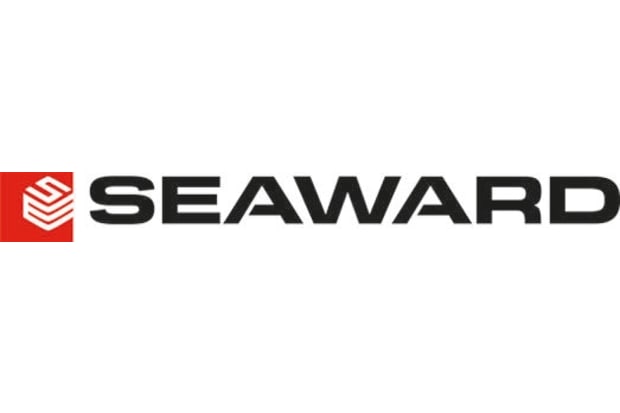
Seaward
Designed for high precision and accuracy, Seaward PAT testers allow for the identification of electrical safety problems before they occur. Seaward offers everything from basic PASS/FAIL testers to instruments for advanced electrical checking. They also offer a complete range of PAT accessories, ideally suited to your PAT testing requirements.
FAQs
What Equipment is Needed for PAT Testing?
The need for equipment will vary, depending on the kind of PAT testing that must be carried out, and the volume of tests that need to be made. A basic PAT insulation test will be sufficient for some appliances with a basic PAT tester being entirely suitable. However, more comprehensive and technical tests may have to be carried out in accordance with the specifications in the IET code of practice. You may also be expected to make use of printers and labels as part of the PAT testing process.
Can I PAT Test My Own Equipment?
Employers have responsibility for electrical appliance testing. However, it's quite common for this duty to be assigned to a ‘competent person’. The competent person should:
- Know how to carry out a visual inspection
- Have sufficient knowledge of electricity
- Know how to complete a PAT test
- Have adequate experience of electrical work
- Understand potential hazards and the necessary precautions to take when PAT testing
- Be able to make an informed decision whether it is safe for PAT testing to continue
Professionals expected to perform testing duties will ideally complete the PAT testing course. It will also be necessary to invest in appropriate PAT testing equipment.
How Often Should Equipment Be PAT Tested?
There is no formal legislation specifying the need for PAT testing. However, it is a legal requirement to ensure that electrical equipment is safe and fit for purpose. The expected regularity of PAT testing will depend on the results of workplace risk assessment procedures. When determining the need for PAT testing, the level of risk should also be considered.
These factors should be considered with regards to the regularity of PAT testing:
- Equipment type (portable, hand-held or transportable)
- Equipment class (class 1 or class 2)
- Equipment use (continuous, infrequent, rough)
- How long equipment has been in service (age)
- If equipment is moved around and how frequently
- Competence of personnel using the equipment
- Where equipment is used (outdoors, construction sites, hazardous atmospheres etc)
- Previous test results
- Manufacturer's guidelines and recommendations
- Equipment modifications or repairs
Workplace PAT testing expectations are as follows:
- Offices, shops and hotels – Class 1 devices including IT equipment should be tested every 48 months. Portable equipment such as extension leads should be tested every 24 months. Handheld equipment should be tested every 12 months
- Schools – All class 1 equipment in schools should be PAT tested every 12 months. Class 2 equipment should be tested every 48 months
- Public use equipment – Stationary and IT equipment such as computers should be tested every 12 months. Moveable, portable and handheld equipment falling into class 2 should be tested every 12 months. Moveable, portable and handheld equipment falling into class 1 should be tested every 6 months
- Construction – All 110V equipment used on construction sites should be tested every 3 months
- Industrial – All industrial sites, including commercial kitchens should have portable and handheld equipment tested every 6 months. Stationary, IT and moveable equipment should be tested every 12 months
Why is PAT Testing Important?
PAT testing is key to ensuring adherence to essential safety standards. It's regarded as the easiest and most effective way of ensuring that workplace electrical appliances are safe to use. As previously mentioned, the expected regularity of PAT testing will depend on the categorisation of electrical appliances and the findings of risk assessments.
How Do You Use a PAT Tester?
You should carry out a thorough visual inspection of the electrical item prior to performing the PAT test. This inspection should allow for the identification of defects and issues such as damage to the plug casing, security of connections, and signs of overheating. Once the visual inspection has been completed you may proceed to test the equipment. This may involve testing for earth continuity, insulation resistance, and general functionality. The testing procedure will vary depending on the kit being used. It may be a simple case of disconnecting the electrical item from the main power supply and plugging it into the tester.
Is PAT Testing a Legal Requirement?
There is no specific legislation or regulation stipulating PAT testing requirements. However, the employer or owner of a business has a legal responsibility to ensure that all reasonable steps are taken to ensure the safety of electrical items used by employees and members of the public. Requirements for UK businesses are set out in the Health and Safety at Work Act and the Electricity at Work Regulations. Each states the need to maintain electrical equipment for the prevention of injury and danger.
Where to Next?
Related links
- PAT Tester Accessories
- Seaward 312A966 PAT Testing Label, For Use With Desk Test n Tag Printers
- Seaward 312A953 PAT Testing Printer Cartridge, For Use With Desk...
- What is Insulation Resistance?
- What is RCD Testing?
- What is Load Bank Testing?
- Seaward 339A924 PAT Testing Scanner Prime Test 300 500, 600
- pH Meters