- Published 9 Feb 2024
- Last Modified 9 Feb 2024
- 8 min
Making Industrial Maintenance Sustainable
Sustainable industrial maintenance is vital for helping the environment and for winning in business, and this guide will explain implementing this sustainability.
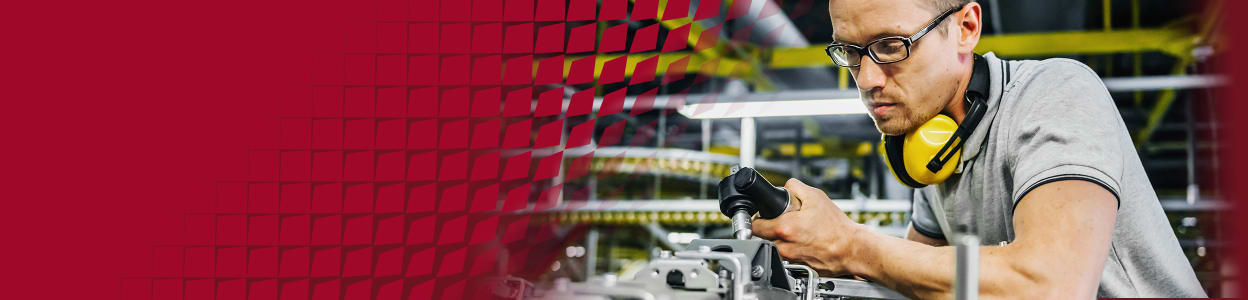
Industrial sustainability is increasingly important as we move away from harmful environmental impacts and towards renewable energy. Maintenance is ripe for these improvements since it regularly consumes and discards parts and industrial fluids. This guide will outline benefits, examples, and implementation of sustainable maintenance that can help your business reduce waste and reduce downtime while keeping your machinery running smoothly.
Importance of Sustainable Maintenance
Sustainable maintenance means improvements in finances, compliance, and reputation. Green maintenance is in essence an effort to reduce waste, something all businesses value.
Environmental Impact
Businesses increasingly recognise the merits of pursuing ESG-minded goals. Identifying your operations’ environmental impact and adopting industrial sustainability improves your reputation and helps your business find its place in the environmentally conscious future.
Sustainable maintenance means fewer parts packaging and filters sent to landfill, using biodegradable products, embracing reusable materials, and improving equipment energy efficiency. All this gives you peace of mind that your business is doing its part to help the world.
Health and Safety Impact
Maintenance practices with negative environmental impacts often also present health and safety hazards. This can include:
- Cleaners and other industrial chemicals being flammable or emitting hazardous fumes
- Noxious fumes from inefficiently burning fuels
- Overly frequent exposure to machinery hazards due to excessive maintenance schedules
A green maintenance plan can make your equipment service safer for your workers and more pleasant to perform. A healthier and safer workplace can also improve your business’ reputation and reduce turnover.
Reduced Costs
Along with meeting ESG goals, sustainable maintenance offers direct business cost savings. A strong CMMS and predictive maintenance plan avoids excessive maintenance sessions and ensures your equipment operates better for longer. This means reducing:
- Consumable spare parts used, such as filters
- Lubricants and cleaners used
- Maintenance shutdowns, letting you reduce downtime
- Maintenance labour costs
- Equipment energy consumption, due to greater energy efficiency and cleaner fuels
- Costly equipment replacement, due to giving machines the care they need when they need it
Compliance with Regulations
Any sustainable maintenance plan will need to keep several factors in line with UK environmental regulations. These cover areas such as:
- Emissions: From industrial machinery engines, building HVAC systems, etc
- Storing hazardous substances: Any cleaners or lubricants considered to be hazardous must be stored safely and with adequate ventilation and spill protection measures in place
- Health and safety: Use of industrial chemical products must mitigate hazards such as flammability, corrosivity, or fumes
- Water: Any runoff into the sewage system must be approved as not unacceptably polluting
- Waste management: Used parts, parts packaging, filters, and fluid containers must be sorted into their appropriate disposal containers, including recycling ones for reusable materials
- Waste storage: Hazardous waste must be stored in proper, secure containers and disposed of by authorised individuals or businesses
Any maintenance plan built around meeting or exceeding these environmental regulations will naturally fall into sustainable maintenance.
Examples of Sustainable Maintenance
Predictive Maintenance
Predictive maintenance is a system of monitoring equipment performance to predict exactly what maintenance each machine requires. This can reduce waste and reduce downtime by only doing the maintenance you need when you need it. That means less grease, oil, and parts consumed, reduced expended energy on post-service startups, and equipment running more efficiently.
With predictive maintenance, sensors installed on equipment give an ongoing picture of the unit’s health. The most common condition monitored in this way is vibrations since irregularities there often indicate a developing problem that could cause a safety incident or costly fixes if unaddressed.
Greener Cleaners
Clean equipment, surfaces, and workspaces are essential for a safe, smooth-running industrial environment. Industrial cleaning products have been solvent-based for many years, meaning they use chemical solvents as their primary cleaning component. These products are certainly effective at cleaning up the stubborn grease and grime of industrial settings, but they pose significant risks. They can be flammable, and they contain volatile organic compounds (VOCs), which are hazardous to inhale. Their significant environmental impact also means that they cost more to properly dispose of under environmental regulations.
Water-based degreasers can be just as effective at industrial cleaning. They are non-flammable, do not give off hazardous fumes, and have fewer environmental concerns regarding disposal.
Water-based degreasers can’t always perform on the level of solvent-based ones, though. Heavy industrial machinery and automotive applications still need the power of solvents for thorough cleaning, so biodegradable products are more suited for less severe scenarios, such as food processing or healthcare. Consider both your cleaning needs and environmental regulations carefully when deciding which industrial cleaners are best for your business.
Efficient Fuels
By changing the quality of fuel your machines consume, they can run with greater energy efficiency and require less maintenance overall. If you have a fleet of diesel vehicles or other diesel-burning equipment, diesel fuel additives can help in the following ways:
- Consuming less fuel
- Lubricating engine parts better, which reduces wear
- Eliminating microbes developed during diesel transportation and storage
- Removing condensed water inside the engine, helping improve efficiency in cold weather
Reduced Waste
Planning a maintenance approach carefully and intentionally can greatly reduce waste generated in maintenance work.
With a predictive maintenance plan and a CMMS, you will only consume filters, oil, and other parts when instruments indicate it’s truly necessary. This means less waste sent to the landfill (both from spent parts and their packaging) and reducing waste fluid that needs careful, costly disposal.
Chemical dosing systems can cut down on the containers and water used for industrial fluids that require dilution. Refillable dosing vessels can dispense the chemicals and water you need into buckets or bottles that aren’t thrown out. This avoids purchases of pre-diluted products and improves safety by avoiding contact with these chemicals. Coupled with a CMMS, this can also let you quantify and control your consumption of water and these products.
Less frequent maintenance also reduces disposable gloves and shop towels going into the bins.
Implementing Sustainable Maintenance
Moving towards green maintenance practices may be a challenge. It will take upfront costs and planning, team commitment, and ongoing monitoring. However, the benefits and merits are well worth it.
Introducing a CMMS
A Computerised Maintenance Management System (CMMS) can go a long way in achieving sustainable maintenance. A CMMS tracks your equipment’s maintenance as well as your inventory. These systems monitor equipment operations and use predictive maintenance to determine when they need to be shut down for service. This lets you reduce downtime and maintenance costs and improve energy efficiency by keeping equipment running smoothly.
A CMMS can also manage your spare parts inventory: how much to stock, when to order more, and when machines will need it. That can lower the environmental impact of stock deliveries and parts packaging, along with reducing the business costs of inventory.
Identifying Wasteful Maintenance
Improving maintenance plans often involves lots of upfront documentation of current operations, and a green maintenance plan in turn will need an assessment of the waste your maintenance currently produces. A CMMS can assist with much of this, but manual recording may also be required.
For each machine, log the following over time:
- Parts such as filters charged to its maintenance
- Fluids charged to its maintenance, including their container sizes
- Frequency of maintenance
- Downtime, and the energy consumed restarting from rest
- Labour charged to maintenance
- Shop supplies consumed, such as disposable gloves
Quantifying Progress
Any system of improvement requires ongoing tracking of measurable, quantifiable goals. With your maintenance waste points identified, establish methods of tracking each one against clearly established goals for reduction. Involve your quality assurance programme to ensure you’re using the best possible methods of recording continual improvement. Cross-reference this data against the dates when you introduced sustainable maintenance measures to get an idea of how well you’re improving your environmental impact. This will reveal which directives are working well and which areas still need improvement.
Employee Commitment
Adopting sustainable maintenance will take commitment from your whole maintenance team. Ensure you train all maintenance staff in the importance and benefits of green maintenance and how their efforts will determine the programme’s success. Explain which of their tasks will change and encourage them to think about the environmental impact of all their day-to-day work.
Training also has to cover analysing the system’s effectiveness. Your CMMS, and even AI, may paint a solid picture of your maintenance efforts, but you’ll still need trained technical staff to assess trends and adjust the maintenance plan accordingly.
If certain tasks are seen as a burden then use encouraging signage and ongoing training to affirm the importance of these measures. Work green maintenance into the company culture so everyone commits to industrial sustainability.
RS can assist with condition monitoring, inventory solutions, and many other areas essential to sustainable maintenance.
Related Articles
Related links
- Sustainable Industrial Waste Management
- Safety Standards in Industrial Maintenance
- Robotics in Industrial Maintenance
- Augmented Reality for Maintenance
- A Guide to Predictive Maintenance Strategy
- How to Create a HVAC Maintenance Plan
- Guide to Industrial Maintenance Tools
- Facom 168 Piece Industrial Maintenance Set Industrial Maintenance...