- Published 22 Nov 2022
- Last Modified 18 Apr 2024
- 8 min
A Guide to Thermal Interface Materials
This guide explores thermal interface materials. It will help you understand the different types and why you might need them. It also outlines which material could be best for your application.

Thermal interface materials are ideal for improving thermal conductivity. The purpose of this guide is to provide a handy overview of thermal interface materials. It explores the differences between thermal pads, grease, and paste. This will help with both using TIMs and choosing the best material for your application.
What are Thermal Interface Materials?
Thermal interface materials (TIMs) fill microscopic irregularities, surface roughnesses, and air gaps between two mating surfaces to aid thermal conduction. It is well known that air is a poor conductor and a highly effective insulator. Therefore, TIMs are designed to increase the efficiency of thermal transfer and offer better cooling, by providing lower thermal contact resistance.
The interface material’s thermal conductivity will largely determine its thermal performance. High thermal conductivity will guarantee good heat transfer, providing the required level of heat dissipation and a more efficient cooling solution.
A suitable thermal interface material should have the following properties:
- High flexibility
- Good insulation
- High compressibility
- Good heat conduction
Thermal interface materials can come in various forms, such as thermal pads, paste, or grease. They are typically easy to handle and set in place, available in multiple thicknesses to suit each application.
What are Thermal Pads?
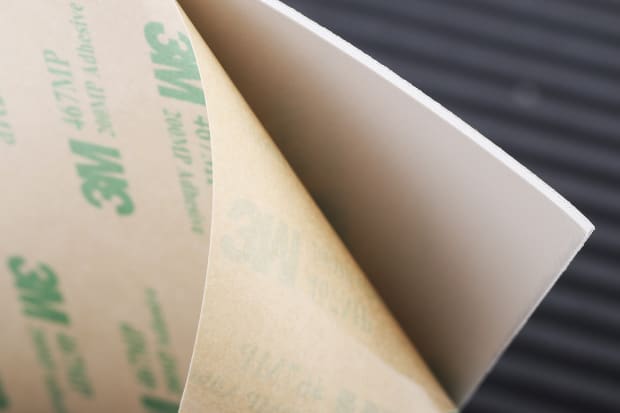
Thermal pads are one type of thermal interface material. These pads provide a thermal interface between PCB components or electronic devices like microprocessors and semiconductors, and heatsinks (devices or substances that absorb excess heat). They are especially useful when conventional thermal pastes or greases cannot be used due to air gaps, rough textures, or uneven surfaces.
Thermal pads come in a variety of thicknesses, softnesses, filler materials, and thermal conductivity. The material used to make the pad will determine the rate of heat transfer. Some materials have much better thermal conductivity, which is measured in Watt per metre Kelvin (WmK).
Thermal pads are also known as gap pads, thermal transfer pads, or thermal gap pads.
Why Do You Need to Use a Thermal Pad?
The purpose of thermal pads is to fill air gaps caused by imperfectly smooth or flat surfaces that need to be in close contact. In contrast, they aren't needed between perfectly flat or smooth surfaces. Heat will be conducted away by the thermal pad, preventing overheating and any potential damage.
Thermal pads have the following advantages:
- It is easy to cut them to the desired size
- Handling them is easy
- There is no pump out or dry out
- Various thicknesses are available
- Humidity and harsh environments do not affect them
Thermal pads have the following disadvantages:
- Delamination is a possibility
- Their thermal conductivity is lower than that of thermal grease
- It is possible for them to cause mechanical stress
- In comparison to thermal grease, they are less effective at filling surface irregularities
- For optimal performance, clamping may be necessary
When Should I Use a Thermal Pad?
Thermal pads can be used in many different applications, including:
- Thermal solutions
- Heating pipes
- Control units
- Memory chips
- Microprocessors
- Engines and automotive
- Supply panels
Effective Resistance

Effective Resistance is the overall barrier to thermal conductivity at an interface. As shown in the equation to the right, it is defined as follows.
- R effective: The bond line thickness
- k TIM: The thermal conductivity of the TIM
- A: The contact area
- R c1: TIM contact resistance at the first surface boundary
- R c2: TIM contact resistance at the second surface boundary
Some components of Effective Resistance, such as contact resistance, can be tricky to calculate. It is possible, however, to minimise them if you understand Effective Resistance.
Additional considerations include:
- Thermal interfaces should have the smallest Effective Resistance possible. The lower the Effective Resistance, the better the heat transfer across the interface
- The thinner the bond line thickness (BLT), the better the heat transfer
- To improve thermal performance, the TIM should have high thermal conductivity
- To fill gaps, materials should have the highest compressive modulus possible. Softer materials will deform to fill irregularities, improving heat transfer. In contrast, more durable materials may be more appropriate for use between two flat, smooth surfaces, since higher clamping pressure can be applied without excessive deformation.
- The clamping pressure should be as high as possible, depending on the type of TIM used. Heat transfer is enhanced by forcing the TIM into surface gaps or irregularities under higher pressure
Types of Thermal Pads
The term ‘thermal pad’ can typically be used to refer to any non-fluid thermal interface material. This means that there are several different product types encompassed within this category:
- Electrically conductive thermal pads: these pads are not electrically insulated, meaning both heat and electricity can be transferred between the two surfaces or devices. They are typically among the thinnest thermal pad materials
- Non-electrically conductive thermal pads: these pads facilitate heat transfer without being electrically conductive. They are typically thicker to incorporate the electrical insulation material, which also means they tend to perform slightly less effectively from a thermal standpoint so should only be used if the need for electrical isolation is important
- Thermal pads for well-matched surfaces: these pads can be either electrically or non-electrically conductive, but they are designed for relatively smooth, well-matched surfaces. They are thinner and lighter than their counterparts for poorly matched surfaces
- Thermal pads for poorly matched surfaces: these pads are specifically designed to fill irregular or large gaps between components. They are usually thick and solid, meaning they are unsuitable for use on well-matched surfaces where a better thermal transfer is required
How Long Do Thermal Pads Last?
Thermal pads will degrade over time and the potential for reduced performance should be considered. The frequency of this degradation will depend on several influencing factors such as the heat they have been subjected to, and in what environment.
There are several reasons for TIM performance degradation:
- Natural degradation over time
- Dry out – a term used to describe a loss of conformability, preventing the pad from moving during thermal expansion and contraction to maintain contact with the surfaces
- Pump out – a term used to describe the TIM being squeezed out of the interface due to the ongoing process of thermal expansion and contraction. Although this issue doesn’t affect thermal pads, it can impact other TIMs like thermal paste and greases
However, it’s also worth bearing in mind that thermal pads are a one-stop solution. If ever the heatsink is removed from its mounted position, the pad will need to be replaced. This is because the heat of the operating CPI will cause the thermal pad to conform to the top, creating new gaps between the surfaces if the heatsink is removed.
What is the Difference Between Thermal Pads and Thermal Paste?
Both thermal pads and thermal grease offer many advantages, but it can be difficult to know which is the best choice for certain applications or environments. When it’s a choice between thermal pads vs thermal paste, which is the better solution?
Thermal paste will conform to the surface it’s applied to, filling in all the inconsistencies in the material and removing any air gaps. This will improve thermal conductivity and heat transfer as the paste effectively forms a coating over the surface between the components. By contrast, thermal pads provide a similar function, but may not eliminate the most microscopic air gaps. Paste can adapt to the surface texture, whereas pads will compress to the surface, just not providing quite as tight coverage as thermal paste.
Another difference is in ease of application. Thermal pads are relatively straightforward to use. They typically have a sticky backing that must be peeled off, then the pad can simply be placed into position. With thermal paste, though, the application must be precise to ensure the area is fully covered and avoid getting the paste anywhere other than the surface where it needs to be applied.
Lastly, the durability and longevity of the solution must also be considered. Thermal pads do have a limited lifespan due to the material they are made from. The exact lifespan will vary depending on the quality of the pad as well as external factors like application and environment, but it’s important to be aware that thermal paste or grease will typically last longer than a thermal pad.
However, both options are good solutions for temperature reduction. There is only likely to be approximately half a degree difference between using thermal pads or thermal paste in most standard applications.
Thermal Grease
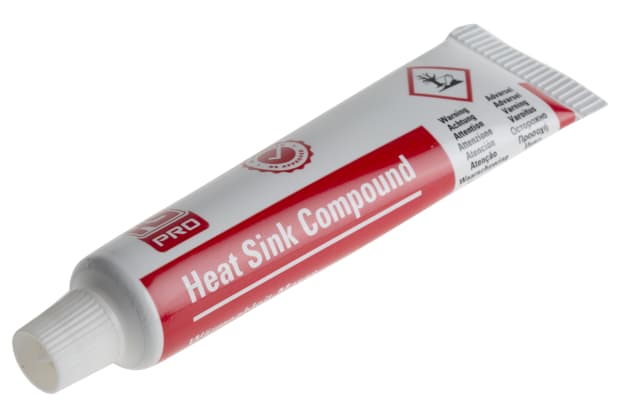
Thermal grease is another form of thermal interface material. It is a soft, room-temperature substance used to transfer heat from a processor to a heatsink more efficiently.
These products are non-curing and should be applied in thin layers to aid thermal transfer. Thermal grease will also readily flow due to its characteristics, so care should be taken during application to avoid mess or process contamination.
There are different types of thermal grease available:
- Ceramic-based
- Metal-based
- Carbon-based
- Liquid-based
In general, thermal grease is not electrically conductive, but some types are designed to be so. Even though most standard applications don't require this, if the grease is used in a circuit where its dielectric properties could have a significant effect, it should be considered.
Thermal grease has the following advantages:
- Curing is not necessary
- High thermal conductivity
- It is possible to fill surface irregularities effectively due to its low viscosity
- Delamination does not occur
Thermal grease has the following disadvantages:
- It can be messy to apply
- Pump-out and phase separation can occur as a result of thermal cycling
- Thickness is difficult to control
- The material can dry out over time
- Excess grease can flow beyond the edges of the assembly
Related Guides
Related links
- RS PRO Thermal Interface Sheet 13W/m·K 150 x 150mm
- Panasonic Thermal Interface Pad 60 x 120mm
- Intelligent LED Solutions Thermal Interface Pad
- Arcol Ohmite Thermal Interface Pad 3W/m·K 49.1x28mm
- Arcol Ohmite Thermal Interface Pad 3W/m·K 48.7x47.5mm
- Arcol Ohmite Thermal Interface Pad 3W/m·K 89.7x72.5mm
- Bergquist 3500ULM Series Self-Adhesive Thermal Interface Pad...
- Bergquist Thermal Interface Pad 3.5W/m·K 28.96 x 20.57mm