- Published 24 Jun 2024
- Last Modified 24 Jun 2024
- 7 min
The Future of Industrial Robotics
In industry, robots have typically been used for welding, handling materials, cutting metal, and packaging food. The future of robotics will see more autonomous, intelligent machines take to the shop floor thanks to the combination of advanced robotics and AI. This guide explains more.
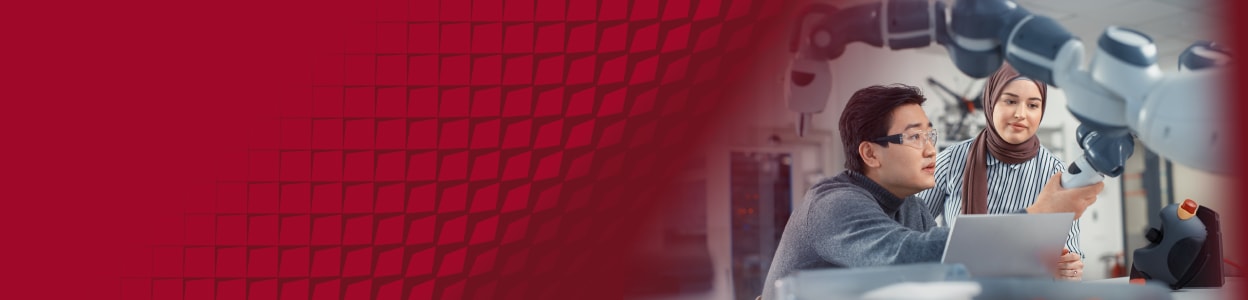
Reviewed by Stephen Bettles, Technical Support Engineer (May 2024)
The use of robotics in manufacturing goes back decades, but what does the future hold when it comes to robots and the sector? The future of robotics is being shaped by developments in technology that are having a widespread impact across industry, such as Big Data and AI. Industrial robots have traditionally been used for tasks such as welding, cutting metal, and packaging food. Today, robots that are smart enough and safe enough to work alongside people – co-bots – are a reality.
It’s no longer the case that robots will just be used to do jobs that are arduous or hazardous for us (although these applications will continue to be important). As robots become more intelligent and autonomous, new possibilities will open up, not just in manufacturing, but also in healthcare, transportation, defence, and entertainment, along with many other industries.
So, how can robots help us in the future? Read on to find out.
Robotics and Industry 4.0
Robotics are one of the key technologies of the fourth industrial revolution, along with Big Data, the Industrial Internet of Things (IIoT), smart factories, and AI. The number of robots used in manufacturing is increasing all the time, with more than 3.4 million industrial robots in the world today. Analysts expect the industrial robot market to more than double in value by 2030 from 2022 levels.
The fourth industrial revolution (Industry 4.0) marks the convergence of physical and digital systems and the use of intelligent machines in manufacturing. Robots are playing a key role thanks to their traditional attributes of speed, repeatability, and efficiency, but are also becoming smarter and capable of conducting more complex tasks.
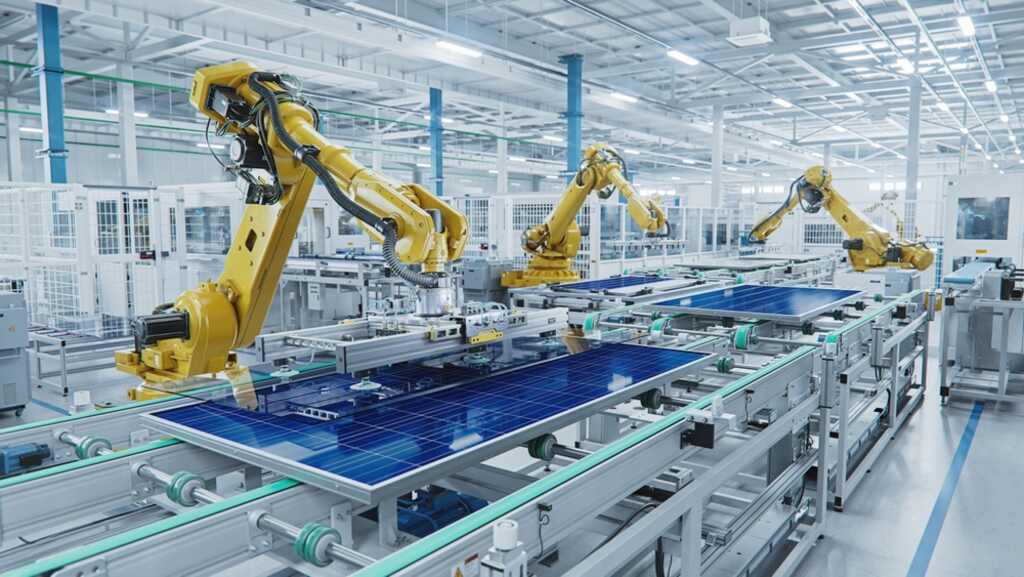
Robotics Trends
Robotics trends include robots that can safely work with people in industry, intelligent robots, humanoid robots, robots that can understand language or navigate complex environments, and robots that can manipulate objects in ever-more sophisticated ways. Key robot trends include:
Robotics and AI
Artificial intelligence is helping automate many processes in business and industry and is proving its worth in analysing enormous data sets in ways that would be difficult or time-consuming for people. AI also has an important role to play in the robots of the future, because it lends robots – traditionally highly efficient, tireless, and rapid beasts of burden for applications such as welding car bodies – human-like abilities, such as identifying and recognising objects in the environment using enhanced computer vision, or manipulating objects in complicated ways.
AI can also allow robots to navigate a factory without the need for human control. It can even comprehend language thanks to the rapid recent development of natural language processing. All these elements will increase the capabilities of industrial robots and their usefulness in the manufacturing environment.
For example, robots that can process language can be programmed more intuitively, without the need for the operator to understand programming languages or how to program PLCs. Robots and AI are highly complementary technologies. AI, in short, is effectively helping to make future robots more human-like.
Autonomous Robots
What will robotics do in the future? A key development will be robots becoming more autonomous and independent of the need for operator intervention.
If a robot is genuinely autonomous, it can operate completely independently. Advances in AI are helping make autonomous robots of this type more commonplace. These innovations include technologies such as computer vision, a field of AI that enables computers to understand image data, and advanced sensors such as laser scanners or cameras, which help robots understand and navigate their environment. For example, autonomous robots are being used in logistics applications for the transport of heavy goods over long distances (such as within very large warehouses).
These autonomous machines for logistics and materials handling can navigate the environment independently, avoid obstacles, and safely deliver goods to the correct location. Autonomous drones are also being used in the manufacturing sector to monitor and inspect parts of the plant that are otherwise difficult to reach.
Co-Bots
Collaborative robots – co-bots – are robots that can work alongside people, which traditionally would have been difficult to achieve due to safety concerns. Co-bots are now being used in automotive, aerospace, healthcare, packaging, and electronics to assist employees. Co-bots typically feature force-sensing technology, which makes them safe for interaction with human workers, along with rounded edges and an array of collision sensors.
These robots may feature robotic arms and control systems that allow them to be guided directly by a human operator (through a handheld device, for example) to perform a task. Unlike autonomous robots, co-bots are specifically designed to be controlled by people, assisting in activities alongside manufacturing personnel. For example, a co-bot can be programmed to deliver raw materials to a production line at given intervals while the engineer focuses on higher-value tasks such as quality control. Co-bots can also be used to assist with activities that may be extremely physically arduous or dangerous for people. Again, AI is helping to make co-bots smarter and capable of more difficult tasks.
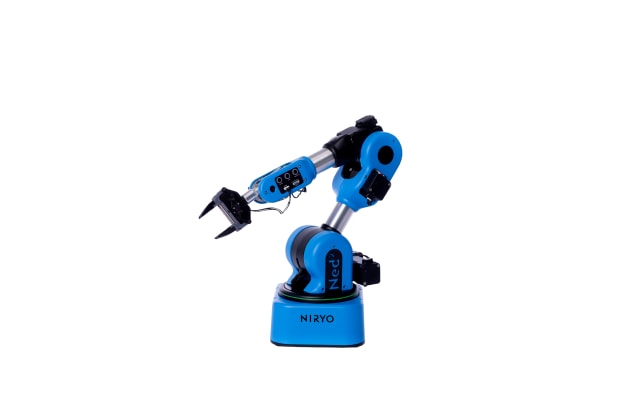
Robotics for Maintenance
Robots also come into their own when it comes to the maintenance of smart factories. They can be used for cleaning and repair, or for detecting leaks of gases or liquids. Maintenance work that is difficult or dangerous for engineers can often be conducted by robots. For example, utilities are experimenting with robots to maintain overhead power lines and gas mains, and robots have been used for a long time to access areas that are completely inaccessible to people, such as nuclear facilities. Autonomous robotic systems can also be used for the inspection of infrastructure such as transport systems or oil and gas pipelines.
Two fields of robotics that are expected to have a special impact on maintenance and repair are very small robotic systems (nanorobotics), which can access extremely confined spaces, and soft, flexible robots that can conduct precision repairs for aerospace. Nanorobotics even promises to conduct repairs without disassembling equipment in some cases.
The Economics of Robotics
Increasing levels of automation are sometimes seen as a threat, but they have a sound economic rationale. Industrial robots are notable for improving productivity, which is why they have found favour in so many manufacturing contexts. Indeed, one of the key measures of the effect of increased automation in manufacturing is that as robot density increases, so does labour productivity. Robotics can have the effect of making a smart factory more efficient and profitable as a result.
Engineers looking at the introduction of robotics into the production environment should consider the return on investment of the robot – how long will it take for the new machinery to pay for itself? Long-term cost depends on not just the upfront cost of the robot but also on maintaining it throughout its life. New robots may cost hundreds of thousands of pounds for some applications, so adopting a refurbished robot may also be an option.
The business case for automation has improved as robot costs have dropped and labour costs have increased. Engineering in the UK is also suffering from chronic skills shortages. Automating tasks that were formerly conducted by people is one way of getting around a widespread shortage of engineers and technicians.
Robotics: The Long-Term View
The long-term future of robots will be one of ever-more sophisticated and capable machines helping transform a range of sectors, from manufacturing to healthcare. This increasing sophistication is being powered by the rapid development of AI, which will lead to smarter, more autonomous robots conducting tasks that were formerly only suitable for people.
While robots have already proved their value in doing arduous and repetitive manufacturing jobs more quickly and tirelessly than people, intelligent robots in the future will be capable of conducting jobs that require advanced decision-making skills and sensitivity to the environment. While the onward advance of automation will see some jobs disappear, manufacturers that successfully introduce advanced robotics can expect to create new roles and free up employees for upskilling to more rewarding work, all while improving profitability and productivity and boosting innovation.
What will robots do in the future? The potential of robotics for the manufacturing sector looks limitless.
Learn more about RS’ range of workplace automation equipment.
Related Articles
Related links
- The Future of Automation – A Guide to What’s Next
- The Future of OEM: Industry Trends
- Industry 4.0 and the Future of Maintenance
- Smart Manufacturing and Sustainable Energy
- Guide to the Future of UK Renewable Energy
- The future of industry 4.0
- A Guide to the Future of Wire and Cable Management
- The Industrial IoT and Smart Factories